Компания JTM Intelligent Equipment Co., Ltd.
Токарный станок для лазерной резки с одним верстаком
Токарный станок для лазерной резки с одним верстаком
Технические параметры станка для лазерной резки JTM | |
Тип лазера | Волоконный лазер |
Лазерная рабочая среда | Волоконная оптика |
Лазерная линия | 1060-1080М |
Номинальная выходная мощность | 1500 Вт/3000 Вт/6000 Вт/12000 Вт |
Качество луча | <0,373 Мрад |
Точность осевого позиционирования | 0,03 мм/м≤+0,03 мм/м |
Максимальный диапазон резки | 3*1,5 м/4*1,5 м/6*1,5 м/4*2 м/6*2 м |
Точность изменения положения | 0,03 мм/м≤+0,03 мм/м |
Максимальная скорость движения | 120М/МИН |
Номинальная мощность | Трехфазный переменный ток 380 В 50 Гц |
Электричество | 17,3 кВт |
Общий уровень защиты источника питания | IP54 |
Максимальное ускорение | 1,2G |
Точность позиционирования | ±0,05 мм |
Точность изменения положения | ±0,02 мм |
Рабочее напряжение | 380 В/50 Гц |
Тип охлаждения | Водяное охлаждение |
Примечание. Все параметры являются динамическими и предназначены только для справки. Для получения дополнительной информации, пожалуйста, свяжитесь со службой поддержки клиентов. |
Толщина резки и параметры скорости | |||||||
Материал | Толщина (ММ) | Газ | 1500 Вт | 3000 Вт | 6000 Вт | 12000 Вт | 15000 Вт |
Углеродистая сталь (Q235B) | Скорость (М/МИН) | Скорость (М/МИН) | Скорость (М/МИН) | Скорость (М/МИН) | Скорость (М/МИН) | ||
1 | Азот/Кислород | 26-29 | 47-50 | 58-62 | |||
2 | Азот/Кислород | 7-8 | 21-23 | 31-36 | |||
3 | Азот/Кислород | / | 6-12 | 18-22 | 32-38 | 34-39 | |
Кислород | 2,9-3,2 | 3,9-4,1 | / | / | / | ||
4 | Азот/Кислород | / | / | 11-13 | 22-26 | 25-29 | |
Кислород | 2,4-2,6 | 3,4-3,6 | 3.7-4 | / | / | ||
5 | Азот/Кислород | / | / | 8-10 | 17-20 | 18-22 | |
Кислород | 1,8-2,0 | / | 3,2-3,3 | / | / | ||
6 | Воздух | / | / | 5,5-6,5 | 12-14 | 16-18 | |
Азот | / | / | 5,5-6,5 | 11-13 | 15-17 | ||
Кислород | 1,6-1,8 | 2,7-2,8 | 2,6-2,8 | 2,6-2,8 | 2,6-2,8 | ||
8 | Воздух | / | / | / | 8-10 | 10-11 | |
Азот | / | / | / | 7-9 | 9-10 | ||
Кислород | 1,1-1,3 | 2,1-2,3 | 2,5-2,6 | 2,5-2,6 | 2,5-2,6 | ||
10 | Воздух | / | / | / | 5-6 | 7-8 | |
Азот | / | / | / | 4,5-5,5 | 6,5-7 | ||
Кислород | 0,9-1,0 | 1,4-1,6 | 2,2-2,3 | 2,2-2,3 | 2,2-2,3 | ||
12 | Воздух | / | / | / | 4.2-5 | 5,5-6,5 | |
Азот | / | / | / | 4-4,8 | 5-6 | ||
Кислород | 0,8-0,9 | 1-1,1 | 1,8-2,0 | 1,9-2 | 1,9-2 | ||
14 | Воздух | / | / | / | 3,5-4,2 | 5-5,55 | |
Азот | / | / | / | 3,2-3,5 | 4,8~5 | ||
Кислород | 0,6-0,7 | 0,9-0,95 | 1,4-1,7 | 1,5-1,6 | 1,5-1,6 | ||
16 | Воздух | / | / | / | / | / | |
Кислород | 0,5-0,6 | 0,8-0,95 | 1,2-1,3 | 1,4-1,6 | 1,4-1,6 | ||
18 | Воздух | / | / | / | / | / | |
Кислород | / | 0,7-0,72 | 0,7-0,8 | 1,4-1,5 | 1,4-1,5 | ||
20 | Воздух | / | / | / | / | / | |
Кислород | / | 0,6-0,65 | 0,6-0,65 | 1,4-1,5 | 1,4-1,5 | ||
22 | Кислород | / | 0,55 | 0,55-0,6 | 1.2 | 1,2-1,3 | |
25 | Кислород | / | 0,5 | 0,5-0,55 | 1 | 1,2-1,3 | |
30 | Кислород | / | / | / | 0,4 | 0,8~0,9 | |
35 | Кислород | / | / | / | 0,35 | 0,4 | |
40 | Кислород | / | / | / | 0,3 | 0,35 | |
45 | Кислород | / | / | / | 0,2 | 0,25 | |
50 | Кислород | / | / | / | / | 0,2 | |
60 | Кислород | / | / | / | / | / | |
70 | Кислород | / | / | / | / | / | |
80 | Кислород | / | / | / | / | / | |
Нержавеющая сталь (SUS 304) | Толщина (ММ) | Газ | 1500 Вт | 3000 Вт | 6000 Вт | 12000 Вт | 15000 Вт |
Скорость (М/МИН) | Скорость (М/МИН) | Скорость (М/МИН) | Скорость (М/МИН) | Скорость (М/МИН) | |||
1 | Азот/Кислород | 27-30 | 50-53 | 59-65 | / | / | |
2 | Азот/Кислород | 8-9 | 23-25 | 32-38 | / | / | |
3 | Азот/Кислород | 4,2-4,5 | 10-12 | 20-24 | 32-38 | 34-39 | |
4 | Азот/Кислород | 2,0-2,2 | 6-8 | 12-15 | 22-26 | 25-29 | |
5 | Азот/Кислород | 1,5-1,7 | / | 9-11 | 17-20 | 18-22 | |
6 | Воздух | 1,0-1,2 | 2,9-3,1 | 6-7,5 | 14-16 | 17-20 | |
Азот | 1,0-1,2 | 2,9-3,1 | 6-7,5 | 13-15 | 16-19 | ||
8 | Воздух | 0,5-0,6 | 1,2-1,3 | 4-4,5 | 10-12 | 12-14 | |
Азот | 0,5-0,6 | 1,2-1,3 | 4-4,5 | 9-11 | 11-13 | ||
10 | Воздух | / | 0,75-0,8 | 2,2-2,4 | 8-9 | 8-10 | |
Азот | / | 0,75-0,8 | 2,2-2,4 | 7,5-8 | 7-9 | ||
12 | Воздух | / | 0,5 | 1,3-1,5 | 6,0-6,5 | 7,0-7,5 | |
Азот | / | 0,5 | 1,3-1,5 | 5,2-6,0 | 6,0-6,5 | ||
14 | Воздух | / | / | 0,9-1,0 | 3,7-4,0 | 4,8-5,0 | |
Азот | / | / | 0,9-1,0 | 3,2-3,5 | 4,3-4,5 | ||
16 | Воздух | / | / | 0,8-0,85 | 2,7-3,0 | 3,4-3,8 | |
Азот | / | / | 0,8-0,85 | 2,3-2,5 | 3,0-3,5 | ||
18 | Воздух | / | / | / | 2,2-2,5 | 3,0-3,3 | |
Азот | / | / | / | 1,8-2,0 | 2,6-2,8 | ||
20 | Воздух | / | / | 0,5-0,6 | 1,6-1,8 | 2,0-2,2 | |
Азот | / | / | 0,5-0,6 | 1,3-1,5 | 1,6-1,8 | ||
25 | Воздух | / | / | / | 0,8-1,0 | 1,2-1,5 | |
Азот | / | / | / | 0,7-0,8 | 1,1-1,3 | ||
30 | Воздух | / | / | / | 0,65 | 0,6-0,7 | |
Азот | / | / | / | 0,25 | 0,33-0,35 | ||
35 | Азот | / | / | / | / | / | |
40 | Азот | / | / | / | 0,15 | 0,25 | |
50 | Азот | / | / | / | 0,1 | 0,15 | |
60 | Азот | / | / | / | / | 0,1 | |
70 | Азот | / | / | / | / | 0,06 | |
80 | Азот | / | / | / | / | / | |
90 | Азот | / | / | / | / | / | |
100 | Азот | / | / | / | / | / | |
Алюминий | Толщина (ММ) | Газ | 1500 Вт | 3000 Вт | 6000 Вт | 12000 Вт | 15000 Вт |
Скорость (М/МИН) | Скорость (М/МИН) | Скорость (М/МИН) | Скорость (М/МИН) | Скорость (М/МИН) | |||
1 | Азот/Воздух | 21-23 | 40-43 | 43-46 | / | / | |
2 | Азот/Воздух | 5-7 | 16-18 | 26-28 | / | / | |
3 | Азот/Воздух | 3,2-3,5 | 8-10 | 6-6,5 | 27-30 | 28-32 | |
4 | Азот/Воздух | 1,5-1,7 | 5-6 | 4,5-5 | 19-21 | 20-22 | |
5 | Азот/Воздух | 0,5-0,7 | / | 2,8-2,9 | 14-16 | 16-18 | |
6 | Азот/Воздух | / | 1,5-2 | 1,7-1,8 | 10-12 | 12-14 | |
8 | Азот/Воздух | / | 0,6-0,7 | 1,0-1,2 | 7-8 | 8-9 | |
10 | Азот/Воздух | / | / | 0,7-0,9 | 4-5 | 5,5-6 | |
12 | Азот/Воздух | / | / | 0,5-0,6 | 2,5-3 | 3,5-4 | |
14 | Азот/Воздух | / | / | / | 2,3-2,5 | 2,5-3 | |
16 | Азот/Воздух | / | / | / | 1,6-1,8 | 1,8-2 | |
18 | Азот/Воздух | / | / | / | 1-1,2 | 1,4-1,6 | |
20 | Азот/Воздух | / | / | / | 0,8 | 0,9-1,0 | |
22 | Азот/Воздух | / | / | / | 0,5 | 0,8 | |
25 | Азот/Воздух | / | / | / | / | 0,5 | |
30 | Азот/Воздух | / | / | / | / | / | |
40 | Азот/Воздух | / | / | / | / | / | |
50 | Азот/Воздух | / | / | / | / | / | |
Латунь | Толщина (ММ) | Газ | 1500 Вт | 3000 Вт | 6000 Вт | 12000 Вт | 15000 Вт |
Скорость (М/МИН) | Скорость (М/МИН) | Скорость (М/МИН) | Скорость (М/МИН) | Скорость (М/МИН) | |||
1 | Азот/Воздух | 18-20 | 37-40 | 41-43 | |||
2 | Азот/Воздух | 4-5 | 14-16 | 24-26 | |||
3 | Азот/Воздух | 2,3-2,5 | 7-9 | 13-14 | 25-28 | 25-29 | |
4 | Азот/Воздух | 1,2-1,4 | 3-4 | 9-10 | 16-18 | 18-20 | |
5 | Азот/Воздух | / | / | 5-6 | 12-14 | 13-16 | |
6 | Азот/Воздух | / | 1,2-1,5 | 4-4,5 | 9-11 | 11-13 | |
8 | Азот/Воздух | / | 0,5-0,6 | 2,3-2,5 | 6-7 | 7-8 | |
10 | Азот/Воздух | / | / | 1,5-1,6 | 3,5-4,5 | 5-5,5 | |
12 | Азот/Воздух | / | / | 1,0-1,2 | 2,2-2,8 | 3,2-3,5 | |
14 | Азот/Воздух | / | / | 0,7-0,9 | 1,8-2 | 2,3-2,8 | |
16 | Азот/Воздух | / | / | 0,5-0,6 | 1,4-1,6 | 1,5-1,8 | |
18 | Азот/Воздух | / | / | / | 0,8-1,0 | 1,1-1,3 | |
20 | Азот/Воздух | / | / | / | 0,7 | 0,7-0,9 | |
22 | Азот/Воздух | / | / | / | 0,4 | 0,7 | |
25 | Азот/Воздух | / | / | / | / | 0,4 | |
1. В данных резки диаметр сердцевины выходного волокна лазера мощностью 1500 Вт составляет 50 микрон. | |||||||
2. В данных режимах резки используется режущая головка Jia qiang, а оптическое соотношение составляет 100/125 (фокусное расстояние коллимирующей фокусирующей линзы). | |||||||
3. Режущий вспомогательный газ: жидкий кислород (чистота 99,99%), жидкий азот (чистота 99,999%), воздух (масло, вода и фильтрация). | |||||||
4. Давление воздуха в этих данных резки относится конкретно к контролируемому давлению воздуха на режущей головке. | |||||||
5. Из-за различий в конфигурациях оборудования и процессах резки (станки, водяное охлаждение, окружающая среда, сопла режущего газа, давление газа и т. д.), используемые разными клиентами. | |||||||
6. Все параметры являются динамическими и предназначены только для справки. Для получения дополнительной информации, пожалуйста, свяжитесь со службой поддержки клиентов. |
Лазерная система мощного станка для лазерной резки является основным компонентом всего устройства. Принцип работы заключается в обеспечении нормальной работы лазера и создании высокоэнергетического лазерного луча с малой шириной импульса за счет совместной работы различных компонентов, который затем облучается на поверхность металлического материала для резки.
Лазер: Лазер является основным компонентом станка для лазерной резки. Его функция заключается в преобразовании электрической энергии в оптическую энергию и производстве лазерного луча высокой энергии. В зависимости от природы и мощности лазеры можно разделить на различные типы, такие как лазеры на углекислом газе, волоконные лазеры, дисковые лазеры и т. д. Среди них волоконные лазеры стали основным выбором для современных мощных станков для лазерной резки из-за их высокая эффективность и надежность.
Источник питания: Блок питания является источником энергии лазера. Он преобразует электрическую энергию в электрическую энергию высокой энергии, необходимую лазеру для излучения света. Технические характеристики и производительность источника питания различаются в зависимости от типа лазера. Как правило, в мощных станках для лазерной резки используются высокочастотные источники питания, которые обладают преимуществами энергосбережения, высокой эффективности и высокой надежности.
Система охлаждения: во время работы лазер выделяет большое количество тепла. Если тепло не может быть эффективно рассеяно, это может повлиять на производительность и срок службы лазера. Поэтому система охлаждения является важным компонентом лазера. Он отводит тепло от лазера во время работы с помощью ряда охлаждающих устройств, таких как рубашки водяного охлаждения и вентиляторы рассеивания тепла.
Система управления: Система управления в основном отвечает за контроль выходной мощности лазера и регулирование различных параметров лазера, таких как ток, напряжение, частота и т. д., чтобы сделать его выходную мощность более стабильной и надежной. Кроме того, система управления также берет на себя задачу контроля траектории резания и параметров скорости.
Оптическая система мощного станка для лазерной резки фокусирует и настраивает лазерный луч с помощью таких компонентов, как отражатели и линзы, которые могут увеличить плотность мощности лазерного луча и добиться более точных результатов резки. В то же время конструкция и настройка оптической системы оказывают существенное влияние на качество и эффективность лазерной резки, поэтому конструкция и настройка оптической системы являются одним из ключей к лазерной резке.
Отражатель: Отражатель является важным компонентом оптической системы. Его функция — отражать лазерный луч, позволяя ему проходить через режущую головку и освещать поверхность металлического материала. Отражатель обычно изготавливается из оптического стекла или кварцевого стекла с высокой прозрачностью и стабильностью.
Объектив. Объектив — еще один важный компонент оптической системы. Его функция состоит в том, чтобы сфокусировать лазерный луч в пятно меньшего размера, увеличивая плотность мощности лазерного луча. Линза обычно изготавливается из стекла или кварцевого стекла с высоким показателем преломления, что позволяет сжимать лазерный луч до очень маленьких размеров для более точной резки.
Устройство регулировки фокусировки. Устройство регулировки фокусировки является важной частью оптической системы. Его функция — регулировка положения фокусировки и размера лазерного луча. Устройство регулировки фокусировки обычно регулируется механическими или электрическими средствами, способными регулироваться в соответствии с такими параметрами, как толщина металлического материала и скорость резки.
Коллимирующее устройство: Коллимирующее устройство обеспечивает движение лазерного луча по прямой линии, позволяя лазерному лучу точно освещать поверхность металлического материала. Коллимирующее устройство обычно регулируется с помощью оптических элементов, таких как линзы или отражатели, которые можно регулировать в соответствии с формой и размером металлического материала.
Являясь важным компонентом мощного станка для лазерной резки, система режущей головки в основном включает в себя сопло, фокусирующую линзу и систему обнаружения отслеживания фокусировки. Его принцип работы заключается в содействии лазерной резке металлических материалов посредством создания воздушного потока сопла, фокусировке лазерного луча в пятно с высокой плотностью энергии с помощью фокусирующей линзы, а также контроле и регулировании положения и высоты лазерного луча с помощью фокусирующей линзы. система обнаружения фокусировки и отслеживания для достижения качественной и эффективной резки металла.
Сопло: Сопло является важной частью системы режущей головки. Его функция заключается в создании воздушного потока, помогающего лазерному лучу резать металлические материалы. Сопла бывают разных форм, в том числе параллельные, сходящиеся и конусообразные, и обычно изготавливаются из нержавеющей стали или меди. Концентричность сопла оказывает существенное влияние на качество резки, поэтому сопло обычно выравнивается с лазерной режущей головкой для достижения лучшего поперечного сечения резки.
Фокусирующая линза: Фокусирующая линза фокусирует лазерный луч в пятно с высокой плотностью энергии, что позволяет резать металлические материалы. Линза обычно изготавливается из оптического стекла или кварцевого стекла с высокой прозрачностью и стабильностью. В зависимости от типа лазерного луча существуют различные типы фокусирующих линз, обычно делящиеся на длиннофокусные и короткофокусные, которые подходят для толстых и тонких пластин соответственно.
Система обнаружения отслеживания фокусировки: Система обнаружения отслеживания фокусировки является одной из ключевых технологий обработки лазерной резки. При лазерной резке головка лазерной фокусировки должна постоянно фокусироваться на заготовке. Изменение положения фокуса повлияет на качество резки продукта. Система отслеживания фокусировки обычно состоит из фокусирующей режущей головки и системы датчиков отслеживания. Его функция состоит в том, чтобы контролировать положение точки фокусировки в режиме реального времени с помощью датчиков и автоматически регулировать положение и высоту режущей головки на основе результатов мониторинга, чтобы гарантировать, что фокус лазерного луча всегда находится на заготовке.
Система числового управления действует как центр управления мощным станком для лазерной резки. Он обеспечивает точный контроль и регулировку лазерного луча с помощью таких компонентов, как блок ЧПУ, человеко-машинный интерфейс, интерфейс ввода/вывода и блок управления движением, чтобы обеспечить высококачественную и эффективную резку металла.
Блок ЧПУ: Блок ЧПУ является ядром системы числового программного управления. Он получает введенные пользователем траекторию обработки и технические параметры, рассчитывает и контролирует траекторию обработки лазерного луча в соответствии с заданными программами и алгоритмами. В блоке с ЧПУ обычно используются высокопроизводительные компьютерные чипы и профессиональные алгоритмы управления движением для обеспечения мониторинга и регулировки процесса обработки в реальном времени, обеспечивая качество и эффективность обработки.
Человеко-машинный интерфейс: Человеко-машинный интерфейс действует как мост между пользователем и системой числового программного управления. Он предоставляет дружественный графический интерфейс, который отображает информацию об обработке и параметры операций, позволяя пользователю удобно вводить и выводить операции. Человеко-машинный интерфейс обычно включает в себя такие компоненты, как панель управления, экран дисплея и клавиатуру, где пользователь может вводить пути обработки и технические параметры с помощью клавиатуры, а также просматривать состояние и результаты обработки на экране дисплея или других внешних устройствах.
Интерфейс ввода/вывода: система числового программного управления взаимодействует с внешними устройствами через интерфейс ввода/вывода. Он может передавать путь обработки и технические параметры, введенные пользователем на блок ЧПУ, а также может выводить состояние обработки и результаты на экран дисплея или другие внешние устройства. Кроме того, система числового управления может получать сигналы состояния от внешних устройств через интерфейс ввода/вывода, чтобы обеспечить стабильность и безопасность во время обработки.
Блок управления движением: Блок управления движением отвечает за управление движением лазерного луча в системе числового программного управления. Он контролирует действия и скорость лазера на основе инструкций, выдаваемых блоком ЧПУ, одновременно отслеживая положение и состояние лазерного луча, чтобы обеспечить точность и стабильность во время обработки. В блоке управления движением обычно используются профессиональные алгоритмы управления движением и высокопроизводительное оборудование управления, обладающее характеристиками высокой точности и эффективности.
Вспомогательная система мощного станка для лазерной резки оказывает важное влияние на стабильность и эффективность резки всего оборудования. В основном он включает в себя систему водяного охлаждения, вспомогательный газ и завесу защитного газа.
Система водяного охлаждения. В мощных станках для лазерной резки лазеры должны работать непрерывно и эффективно, поэтому необходимо соответствующее охлаждение. Система водяного охлаждения предназначена для удовлетворения этого требования путем охлаждения лазера через специальные каналы охлаждающей воды, обеспечивая его нормальную работу. Особенно важно отметить, что качество и расход охлаждающей воды оказывают существенное влияние на охлаждающий эффект и срок службы оборудования, поэтому необходимо регулярное техническое обслуживание и замена.
Вспомогательный газ: Вспомогательный газ играет важную роль при лазерной резке. Во время лазерной резки вспомогательный газ помогает сдувать шлак, защищать линзу режущей головки от загрязнения, а также помогает улучшить скорость и качество резки. Вообще говоря, разные вспомогательные газы по-разному воздействуют на разные металлические материалы, поэтому соответствующий вспомогательный газ следует выбирать в соответствии с типом металлического материала и требованиями резки.
Защитная газовая завеса: Защитная газовая завеса в основном защищает головку лазерной резки. Во время лазерной резки завеса защитного газа может эффективно предотвращать реакции между кислородом, азотом и другими вспомогательными газами с металлическим материалом при высоких температурах, тем самым влияя на качество резки. В то же время защитная газовая завеса также может предотвратить перелив лазерного луча, избегая вреда операторам.
Рабочий процесс станка лазерной резки выглядит следующим образом:
Входная графика: графика, подлежащая вырезанию, вводится в компьютер в виде программного обеспечения CAD или CAM. Этот шаг можно выполнить путем рисования вручную или импорта существующих файлов САПР. При вводе графики необходимо обеспечить точность и точность графики, чтобы последующий процесс резки протекал гладко.
Компьютерное проектирование (CAD/CAM): использование специального программного обеспечения на компьютере для проектирования, компоновки и оптимизации входной графики. На этом этапе необходимо учитывать размер, форму, толщину материала, а также форму и размер необходимой резки. Программное обеспечение CAD/CAM помогает нам редактировать, изменять и улучшать графику в соответствии с потребностями и требованиями различных клиентов.
В программном обеспечении CAD/CAM можно выполнять такие операции, как графическое рисование, модификацию, удаление, вращение, масштабирование, а также графическую компоновку и оптимизацию для обеспечения эффективности и точности резки. Кроме того, программное обеспечение CAD/CAM может предоставлять функции трехмерного моделирования, которые могут лучше продемонстрировать внешний вид и структуру продукта, помогая клиентам лучше понять продукт.
После завершения проектирования CAD/CAM данные о траектории резки можно вывести и передать на станок для лазерной резки с числовым программным управлением для операций резки. Таким образом, точность и аккуратность программного обеспечения CAD/CAM напрямую влияют на качество и точность резки. Поэтому при использовании программного обеспечения CAD/CAM для проектирования необходимы осторожность и точность, чтобы обеспечить хорошие результаты резки.
Оптическая регулировка пути — это важный шаг, который включает в себя настройку пути и параметров лазерного луча в соответствии с разработанной графикой, чтобы гарантировать, что лазерный луч может точно освещать желаемое положение резки. Эти шаги включают в себя:
Регулировка мощности лазера: Мощность лазера является одним из важных факторов, влияющих на эффект резки. Чтобы лазерный луч мог точно разрезать материал, мощность лазера необходимо отрегулировать в соответствии с графическим дизайном и свойствами материала. Регулировка мощности лазера может быть достигнута путем изменения тока или напряжения лазера.
Регулировка размера и формы пятна: Пятно — это световое пятно на поверхности материала, генерируемое лазерным лучом, его размер и форма также оказывают важное влияние на эффект резки. Чтобы лазерный луч точно освещал желаемое положение резки, необходимо отрегулировать размер и форму пятна. Обычно размер и форму пятна можно регулировать с помощью оптических компонентов, таких как линзы и зеркала.
Регулировка фокусного расстояния и положения фокуса линзы: Фокусное расстояние и положение фокуса линзы оказывают важное влияние на эффект фокусировки лазерного луча и точность резки. Чтобы лазерный луч мог точно сфокусироваться на желаемом положении резки, необходимо отрегулировать фокусное расстояние и положение фокуса. Обычно фокусное расстояние и положение фокусировки можно регулировать, вращая регулировочное кольцо на объективе.
Во время регулировки оптического пути необходимо соблюдать осторожность и осторожность, чтобы обеспечить точность настройки каждого параметра. В то же время необходимо провести необходимые испытания и проверки, чтобы гарантировать, что лазерный луч может точно освещать желаемое положение резки. Как правило, для обеспечения стабильных и точных результатов резки оптическая регулировка пути должна выполняться профессиональными техническими специалистами или опытными операторами.
Пробная резка — важный шаг перед формальной резкой на станке для лазерной резки с числовым программным управлением. Его цель – проверить точность и скорость резки, чтобы убедиться в их соответствии предъявляемым требованиям. Пробная резка может выявить потенциальные проблемы и области для улучшения, предоставляя ориентиры и основу для формального процесса резки.
В процессе пробной резки обычно выбирается тестовый образец, изготовленный из того же или аналогичного материала, что и стандартный режущий материал. Это позволяет лучше оценить эффективность резки и адаптируемость. В процессе пробной резки технический персонал может регулировать такие параметры, как положение и высота режущей головки, мощность лазера и скорость резки, чтобы оптимизировать эффект резки.
Этапы пробной резки включают в себя следующее:
Выбор образца для испытаний: для проведения испытания выберите образец для испытаний, изготовленный из того же или аналогичного материала, что и стандартный режущий материал. Это позволяет лучше оценить эффективность резки и адаптируемость.
Регулировка параметров: на основе свойств материала испытуемого образца и графического дизайна отрегулируйте такие параметры, как положение и высота режущей головки, мощность лазера и скорость резки. Эти настройки параметров можно выполнить с помощью панели управления или программного обеспечения CAD/CAM.
Процесс пробной резки: запустите станок для лазерной резки с числовым программным управлением и проведите пробную резку по заданным траекториям. В процессе пробной резки наблюдайте за качеством и эффективностью резки, в том числе за гладкостью кромок, шероховатостью поверхности среза, наличием зон термического воздействия.
Оценка результата: После завершения пробной резки оцените эффективность резки. Измерьте размер и форму тестового образца и сравните его с проектом САПР, чтобы оценить точность и качество резки. Дополнительно проверьте качество режущих кромок, например, наличие заусенцев или остатков расплава.
Корректировка параметров: По результатам пробной резки внести коррективы в параметры. Если точность и качество резки не соответствуют требованиям, отрегулируйте такие параметры, как оптический путь и другие параметры, чтобы оптимизировать эффективность резки. Например, отрегулируйте мощность лазера, скорость резки, а также положение и высоту режущей головки.
Повторите пробную резку: после настройки параметров проведите еще одну пробную резку, чтобы проверить результаты и осуществимость регулировки. Если точность и качество резки соответствуют требованиям, приступайте к формальному этапу резки.
Пробная резка — это итеративный процесс, который может потребовать нескольких пробных резов и корректировки параметров для достижения идеальной эффективности резки. Во время этого процесса требуется терпение и профессиональное руководство со стороны технического персонала для обеспечения стабильного качества и точности резки.
Формальная резка — это процесс использования станка для лазерной резки с числовым программным управлением для запуска формального процесса резки после пробной резки и настройки параметров. Во время формального процесса резки система числового управления автоматически управляет перемещением лазерного луча по заранее заданной траектории, одновременно отслеживая движение материала, чтобы гарантировать, что лазерный луч может точно вырезать желаемую форму и размер.
Процесс формальной резки включает в себя следующие этапы:
Подготовка: Прежде чем начать формальный процесс резки, необходимо проверить зону резки, чтобы убедиться в отсутствии препятствий или загрязнений. В то же время материал необходимо разместить в правильном положении, а размер и толщину материала необходимо подтвердить, чтобы убедиться, что они соответствуют требованиям.
Настройка параметров: на основе результатов пробной резки и свойств материала установите такие параметры, как мощность лазера, скорость резки и т. д. Эти настройки параметров можно выполнить с помощью панели управления или программного обеспечения CAD/CAM. Кроме того, необходимо настроить траекторию резки и программу, чтобы лазерный луч мог двигаться по заданной траектории.
Начало резки: запустите станок для лазерной резки с числовым программным управлением, и лазерный луч автоматически перемещается под контролем системы числового управления, отслеживая движение материала. В процессе резки лазерный луч облучает поверхность материала, образуя расплавленную и испаренную область для достижения резки.
Мониторинг в реальном времени: во время процесса резки система числового управления контролирует в реальном времени относительное положение между лазерным лучом и материалом, чтобы обеспечить точность и точность резки. Если будут обнаружены какие-либо ошибки или проблемы, система автоматически их скорректирует и исправит.
Завершение резки: Когда резка будет завершена, оборудование автоматически прекратит работу и издаст звуковой сигнал или сигнал. В это время оператор может осмотреть и измерить вырезанные детали, чтобы подтвердить, соответствуют ли качество и точность резки требованиям.
Формальная резка — это высокоточный и высокоэффективный процесс, требующий обеспечения точности и правильности настройки каждого параметра. В то же время операторы должны иметь богатый опыт и навыки, чтобы справляться с непредвиденными ситуациями и соответствовать требованиям различных свойств материалов.
Система охлаждения обычно оснащена станком для лазерной резки с числовым программным управлением, чтобы гарантировать стабильную работу лазера во время процесса резки. Система охлаждения предназначена для эффективного снижения температуры лазера, что позволяет избежать ошибок резки, вызванных колебаниями температуры.
Принцип работы системы охлаждения: Система охлаждения обычно использует водяное или воздушное охлаждение. Система охлаждения с водяным охлаждением использует циркулирующую воду для отвода тепла, выделяемого лазером, и выпуска его наружу через радиатор. В системе охлаждения с воздушным охлаждением используется вентилятор, который нагнетает холодный воздух на лазер и выводит тепло наружу через радиатор.
Состав системы: Система охлаждения обычно состоит из радиатора, водяного насоса или вентилятора, резервуара для воды или фильтра и датчика температуры.
Радиатор и водяной насос или вентилятор. Радиатор и водяной насос или вентилятор являются основными компонентами системы охлаждения с водяным охлаждением. Водяной насос забирает воду из резервуара для воды и течет через лазер, унося тепло, выделяемое лазером. Радиатор отдает тепло наружу и поддерживает температуру воды в определенном диапазоне. В системе охлаждения с воздушным охлаждением вентилятор используется для подачи холодного воздуха на лазер и отвода тепла через радиатор.
Резервуар для воды и фильтр. В системе охлаждения с водяным охлаждением резервуар для воды используется для хранения циркулирующей воды, а фильтр используется для фильтрации примесей в воде, чтобы поддерживать чистоту воды и предотвращать засорение радиатора.
Датчик температуры: Датчик температуры используется для контроля температуры лазера и передачи сигнала температуры в систему управления. Система управления регулирует мощность лазера или рабочее состояние системы охлаждения в соответствии с температурным сигналом, тем самым поддерживая температурную стабильность лазера.
Система охлаждения играет решающую роль в станке для лазерной резки с числовым программным управлением. Он может эффективно снизить температуру лазера, избежать ошибок резки, вызванных колебаниями температуры, и тем самым обеспечить стабильность и точность процесса резки.
Чтобы удовлетворить потребности различных клиентов, станки для лазерной резки с числовым программным управлением обычно имеют множество различных режимов и функций резки, таких как резка с вращением, резка с наклоном, многоосевая связь и т. д. Эти функции могут быть персонализированы и настроены в соответствии с потребностями клиента. для удовлетворения различных требований к резке различных форм и структур.
Резка с вращением — это распространенный режим резки, который позволяет создавать на материале круглые или эллиптические области резки. Контролируя скорость вращения лазерного луча и скорость движения материала, на материале можно формировать круговые или эллиптические зоны резки разных размеров и форм. Этот режим резки подходит для резки круглых или эллиптических деталей, таких как шестерни, подшипники и т. д.
Резка с наклоном также является распространенным режимом резки. Контролируя угол и амплитуду колебаний лазерного луча на поверхности материала, можно вырезать различные формы. Например, контролируя угол колебания влево-вправо и амплитуду лазерного луча на поверхности материала, можно вырезать различные формы прямоугольной, трапециевидной, треугольной и т. д. Этот режим резки подходит для деталей, требующих резки различной формы, например, кронштейнов, направляющих и т. д.
Многоосевая связь — это расширенный режим резки. Управляя движением лазерного луча по нескольким осям на поверхности материала, можно вырезать сложную графику и структуры. Например, управляя движением лазерного луча по осям X, Y и Z, можно вырезать трехмерные конструкции. Этот режим резки подходит для деталей, требующих разрезания на сложные графические объекты и конструкции, таких как автомобильные компоненты, компоненты аэрокосмической отрасли и т. д.
С точки зрения эффективного производства с помощью автоматизированных производственных линий, станки для лазерной резки с числовым программным управлением могут быть интегрированы с другим оборудованием, таким как роботы и конвейерные ленты, для достижения автоматизированного и эффективного производства резки. Благодаря сотрудничеству автоматизированных производственных линий можно значительно повысить эффективность производства, снизить затраты на рабочую силу и гарантировать качество и стабильность продукции. Например, роботы могут автоматически размещать материалы в зоне резки, а ленточные конвейеры могут автоматически транспортировать отрезанные детали к следующему процессу, обеспечивая непрерывное автоматизированное производство и повышая эффективность и качество производства.
Поделиться с
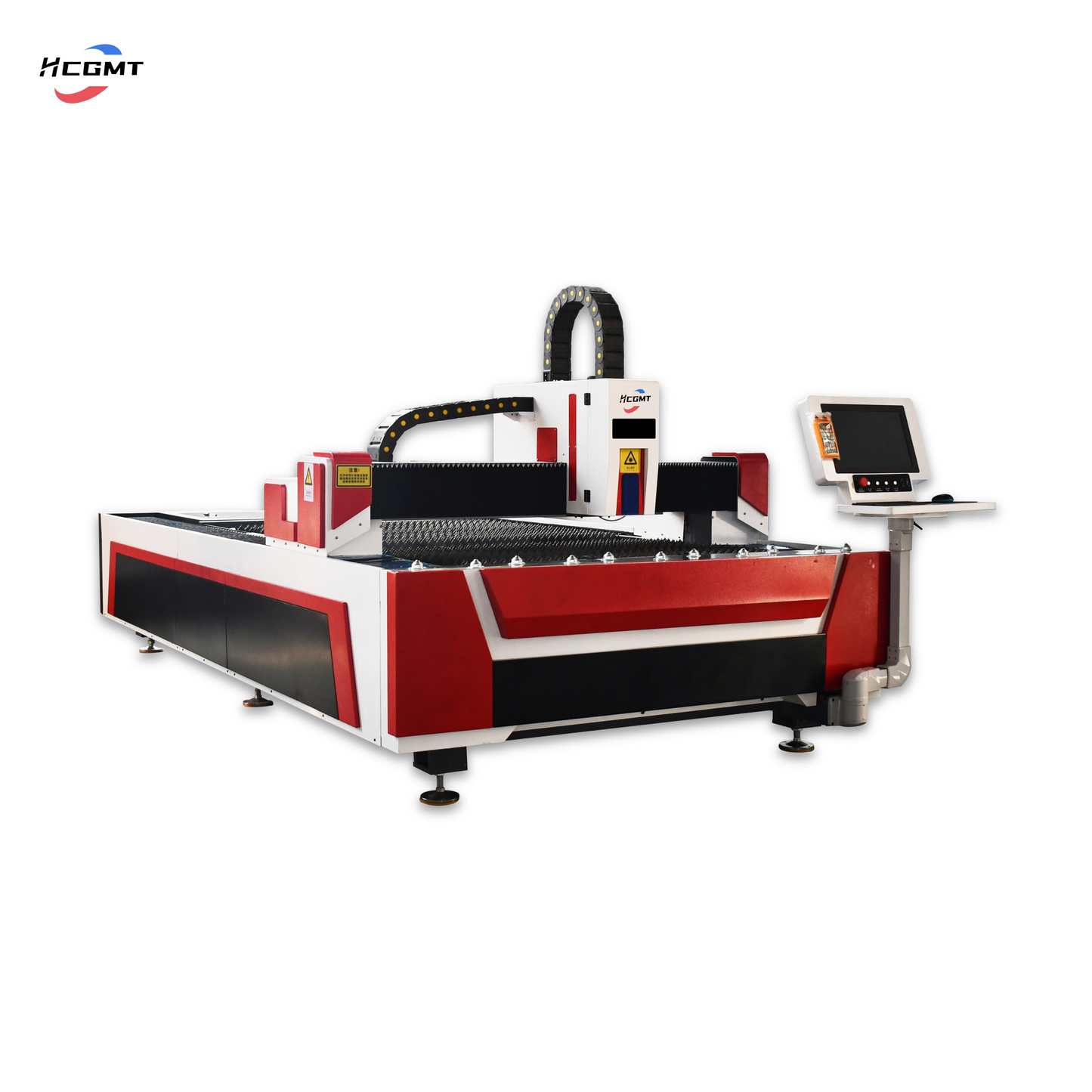
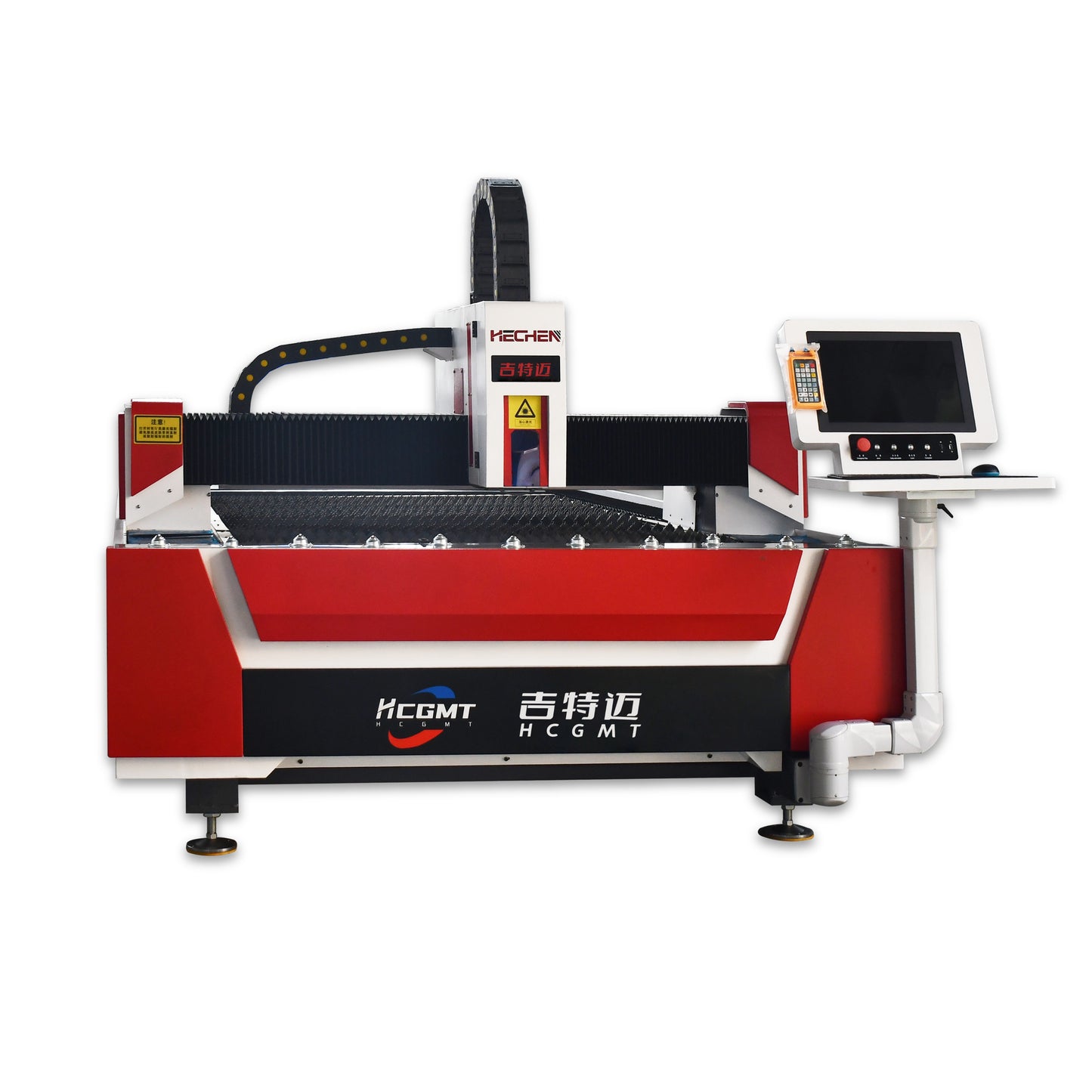
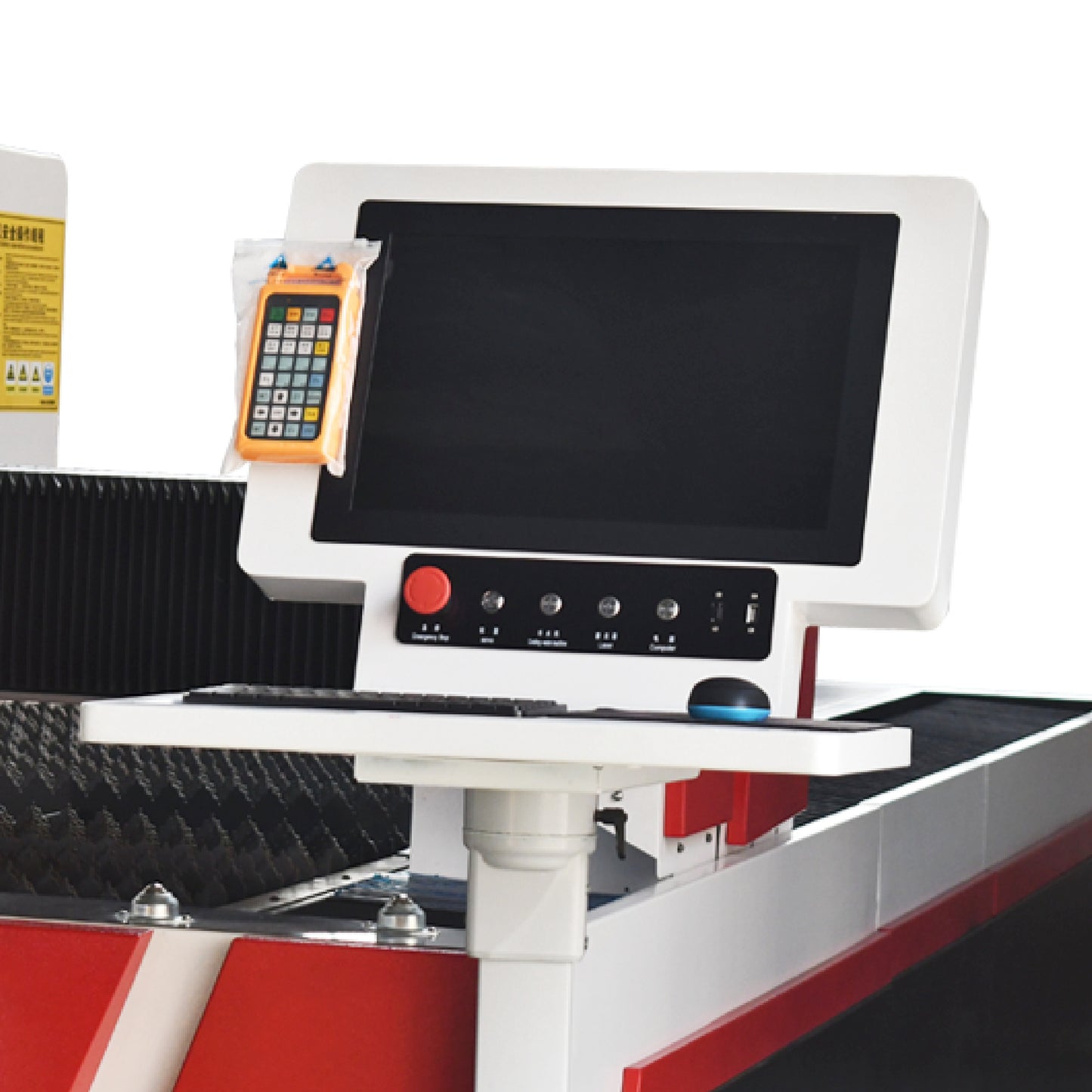
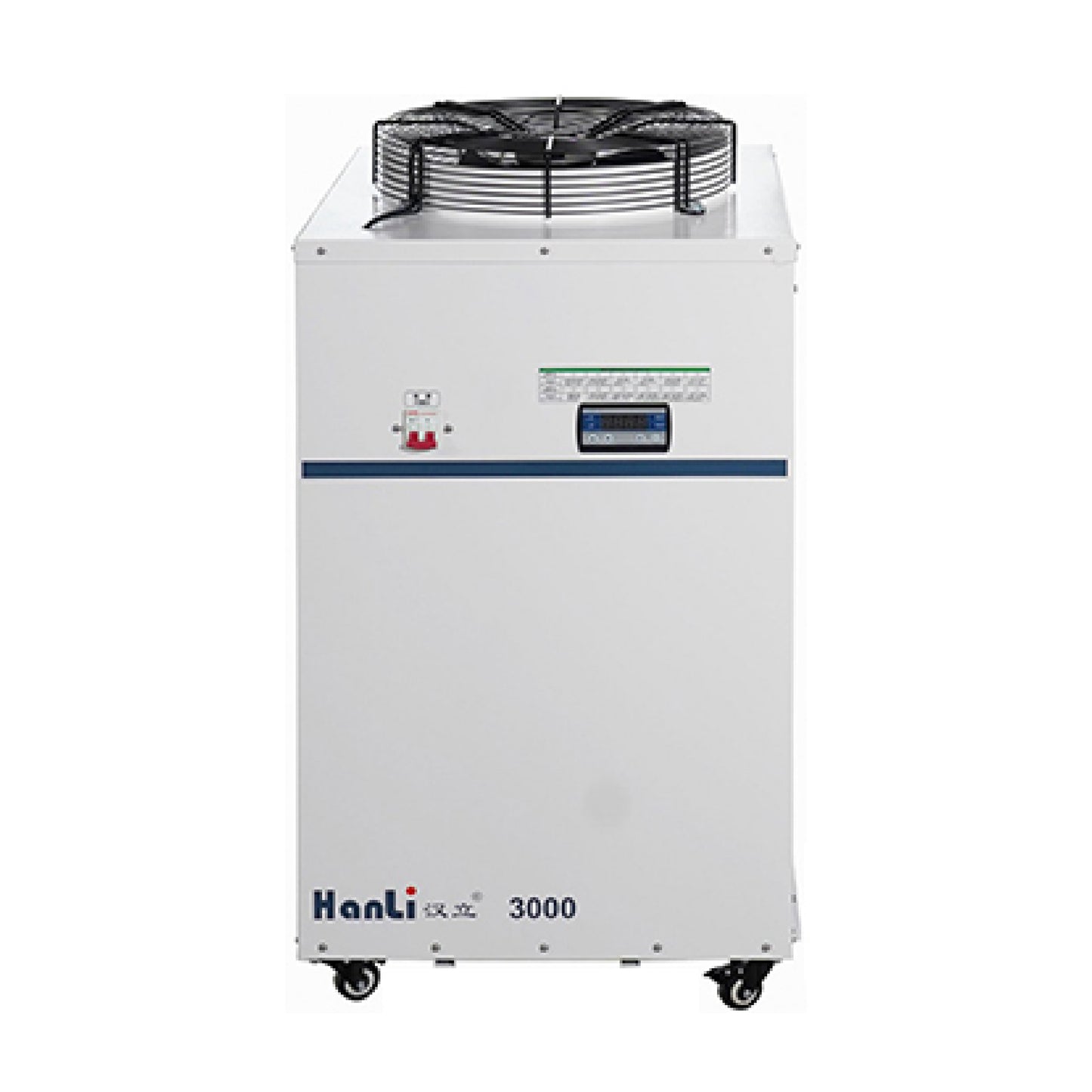
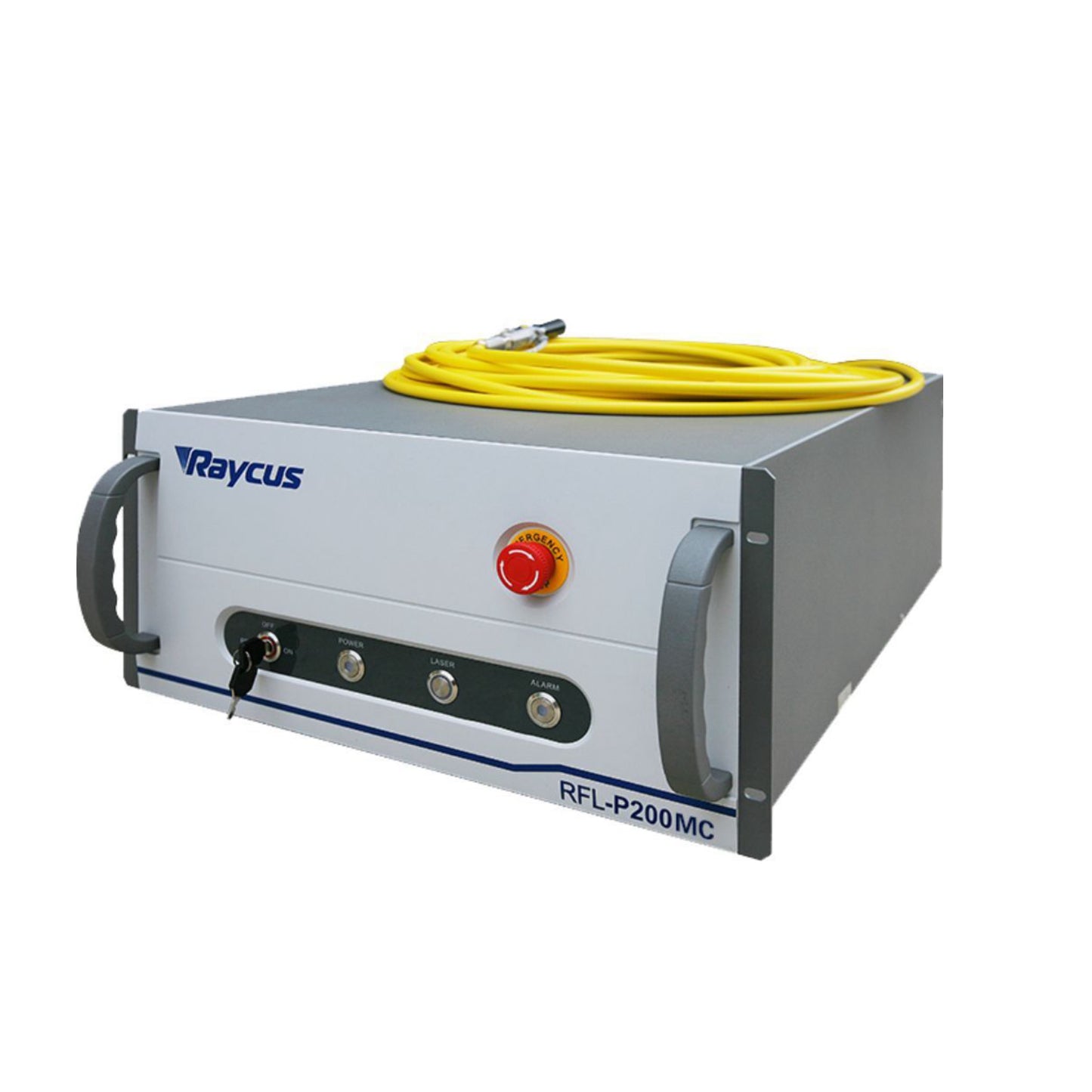
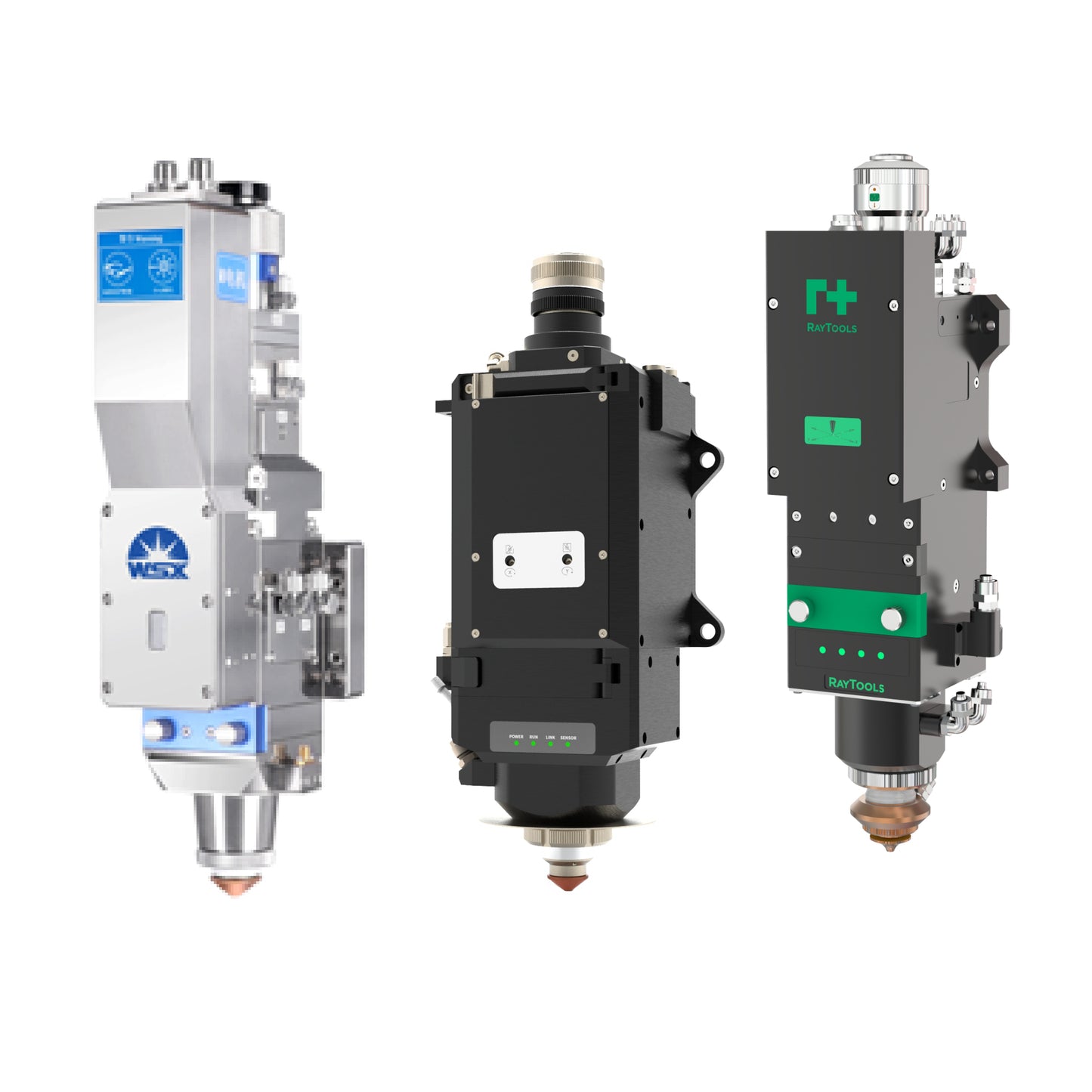
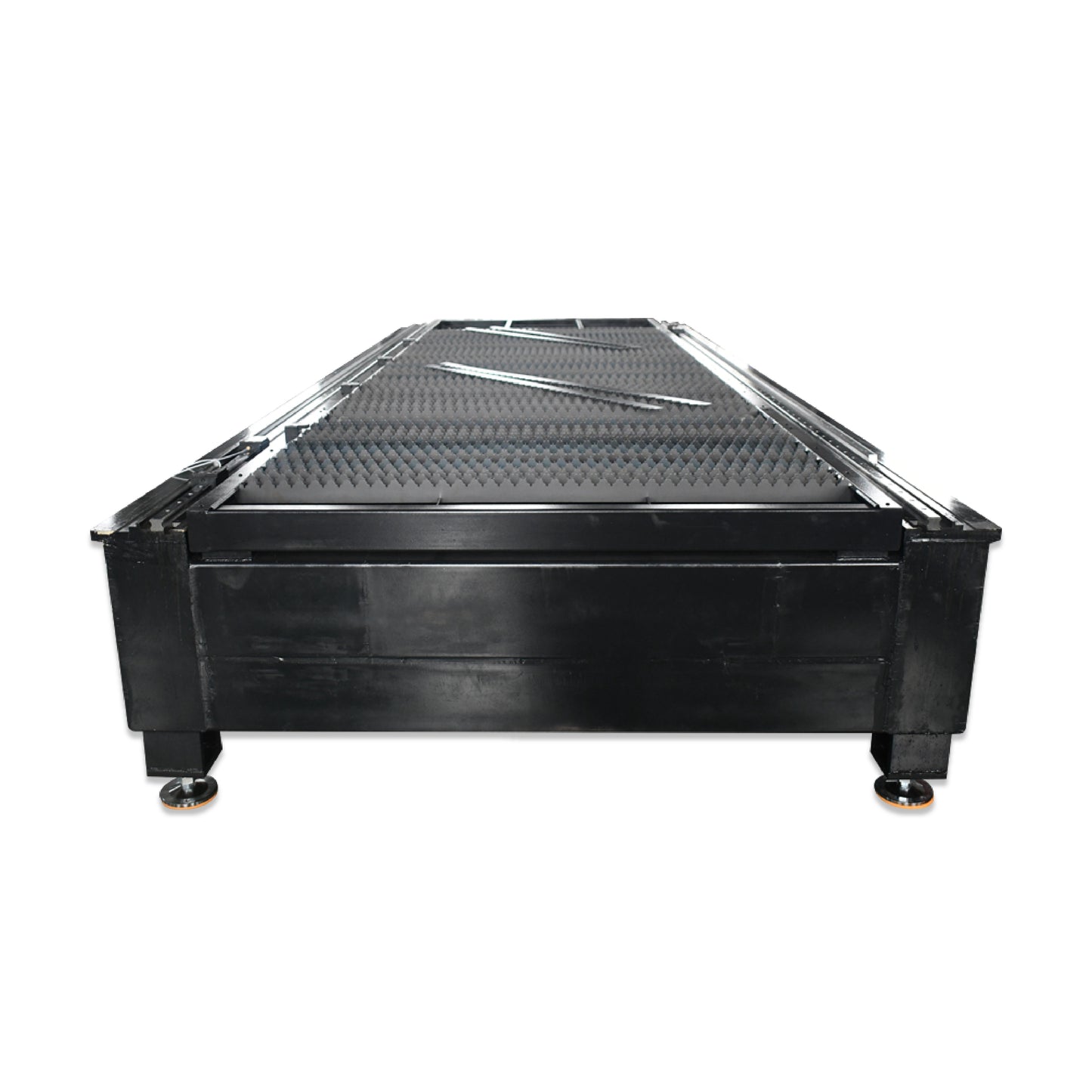