JTM Intelligent Equipment Co., Ltd.
HCGMT® Hydraulic Exchange Workbench Fiber Laser Cutting Machine Customizable
HCGMT® Hydraulic Exchange Workbench Fiber Laser Cutting Machine Customizable
JTM Double Workbench Hydraulic Switching High Power Laser Cutting Machine Technical Parameters |
|
Laser Power | 15000W/20000W/30000W |
Maximum Cutting Range | 6*2.5M/8*2.5M/12*2.5M |
Maximum Moving Speed | 150M/MIN |
Maximum Acceleration | 1.5G |
Positioning Accuracy | ±0.05MM |
Repositioning Accuracy | ±0.02MM |
Operating Voltage | 380V/50HZ |
Cooling Type | Water Cooling |
Note: All parameters are dynamic and for reference only. For more information, please contact customer service. |
Cutting Thickness & Speed Parameters | |||||||
Material | Thickness(MM) | Gas | 1500W | 3000W | 6000W | 12000W | 15000W |
Carbon Steel (Q235B) | Speed (M/MIN) | Speed (M/MIN) | Speed (M/MIN) | Speed (M/MIN) | Speed (M/MIN) | ||
1 | Nitrogen/Oxygen | 26-29 | 47-50 | 58-62 | |||
2 | Nitrogen/Oxygen | 7-8 | 21-23 | 31-36 | |||
3 | Nitrogen/Oxygen | / | 6-12 | 18-22 | 32-38 | 34-39 | |
Oxygen | 2.9-3.2 | 3.9-4.1 | / | / | / | ||
4 | Nitrogen/Oxygen | / | / | 11-13 | 22-26 | 25-29 | |
Oxygen | 2.4-2.6 | 3.4-3.6 | 3.7-4 | / | / | ||
5 | Nitrogen/Oxygen | / | / | 8-10 | 17-20 | 18-22 | |
Oxygen | 1.8-2.0 | / | 3.2-3.3 | / | / | ||
6 | Air | / | / | 5.5-6.5 | 12-14 | 16-18 | |
Nitrogen | / | / | 5.5-6.5 | 11-13 | 15-17 | ||
Oxygen | 1.6-1.8 | 2.7-2.8 | 2.6-2.8 | 2.6-2.8 | 2.6-2.8 | ||
8 | Air | / | / | / | 8-10 | 10-11 | |
Nitrogen | / | / | / | 7-9 | 9-10 | ||
Oxygen | 1.1-1.3 | 2.1-2.3 | 2.5-2.6 | 2.5-2.6 | 2.5-2.6 | ||
10 | Air | / | / | / | 5-6 | 7-8 | |
Nitrogen | / | / | / | 4.5-5.5 | 6.5-7 | ||
Oxygen | 0.9-1.0 | 1.4-1.6 | 2.2-2.3 | 2.2-2.3 | 2.2-2.3 | ||
12 | Air | / | / | / | 4.2-5 | 5.5-6.5 | |
Nitrogen | / | / | / | 4-4.8 | 5-6 | ||
Oxygen | 0.8-0.9 | 1-1.1 | 1.8-2.0 | 1.9-2 | 1.9-2 | ||
14 | Air | / | / | / | 3.5-4.2 | 5-5.55 | |
Nitrogen | / | / | / | 3.2-3.5 | 4.8~5 | ||
Oxygen | 0.6-0.7 | 0.9-0.95 | 1.4-1.7 | 1.5-1.6 | 1.5-1.6 | ||
16 | Air | / | / | / | / | / | |
Oxygen | 0.5-0.6 | 0.8-0.95 | 1.2-1.3 | 1.4-1.6 | 1.4-1.6 | ||
18 | Air | / | / | / | / | / | |
Oxygen | / | 0.7-0.72 | 0.7-0.8 | 1.4-1.5 | 1.4-1.5 | ||
20 | Air | / | / | / | / | / | |
Oxygen | / | 0.6-0.65 | 0.6-0.65 | 1.4-1.5 | 1.4-1.5 | ||
22 | Oxygen | / | 0.55 | 0.55-0.6 | 1.2 | 1.2-1.3 | |
25 | Oxygen | / | 0.5 | 0.5-0.55 | 1 | 1.2-1.3 | |
30 | Oxygen | / | / | / | 0.4 | 0.8~0.9 | |
35 | Oxygen | / | / | / | 0.35 | 0.4 | |
40 | Oxygen | / | / | / | 0.3 | 0.35 | |
45 | Oxygen | / | / | / | 0.2 | 0.25 | |
50 | Oxygen | / | / | / | / | 0.2 | |
60 | Oxygen | / | / | / | / | / | |
70 | Oxygen | / | / | / | / | / | |
80 | Oxygen | / | / | / | / | / | |
Stainless Steel (SUS 304) | Thickness(MM) | Gas | 1500W | 3000W | 6000W | 12000W | 15000W |
Speed (M/MIN) | Speed (M/MIN) | Speed (M/MIN) | Speed (M/MIN) | Speed (M/MIN) | |||
1 | Nitrogen/Oxygen | 27-30 | 50-53 | 59-65 | / | / | |
2 | Nitrogen/Oxygen | 8-9 | 23-25 | 32-38 | / | / | |
3 | Nitrogen/Oxygen | 4.2-4.5 | 10-12 | 20-24 | 32-38 | 34-39 | |
4 | Nitrogen/Oxygen | 2.0-2.2 | 6-8 | 12-15 | 22-26 | 25-29 | |
5 | Nitrogen/Oxygen | 1.5-1.7 | / | 9-11 | 17-20 | 18-22 | |
6 | Air | 1.0-1.2 | 2.9-3.1 | 6-7.5 | 14-16 | 17-20 | |
Nitrogen | 1.0-1.2 | 2.9-3.1 | 6-7.5 | 13-15 | 16-19 | ||
8 | Air | 0.5-0.6 | 1.2-1.3 | 4-4.5 | 10-12 | 12-14 | |
Nitrogen | 0.5-0.6 | 1.2-1.3 | 4-4.5 | 9-11 | 11-13 | ||
10 | Air | / | 0.75-0.8 | 2.2-2.4 | 8-9 | 8-10 | |
Nitrogen | / | 0.75-0.8 | 2.2-2.4 | 7.5-8 | 7-9 | ||
12 | Air | / | 0.5 | 1.3-1.5 | 6.0-6.5 | 7.0-7.5 | |
Nitrogen | / | 0.5 | 1.3-1.5 | 5.2-6.0 | 6.0-6.5 | ||
14 | Air | / | / | 0.9-1.0 | 3.7-4.0 | 4.8-5.0 | |
Nitrogen | / | / | 0.9-1.0 | 3.2-3.5 | 4.3-4.5 | ||
16 | Air | / | / | 0.8-0.85 | 2.7-3.0 | 3.4-3.8 | |
Nitrogen | / | / | 0.8-0.85 | 2.3-2.5 | 3.0-3.5 | ||
18 | Air | / | / | / | 2.2-2.5 | 3.0-3.3 | |
Nitrogen | / | / | / | 1.8-2.0 | 2.6-2.8 | ||
20 | Air | / | / | 0.5-0.6 | 1.6-1.8 | 2.0-2.2 | |
Nitrogen | / | / | 0.5-0.6 | 1.3-1.5 | 1.6-1.8 | ||
25 | Air | / | / | / | 0.8-1.0 | 1.2-1.5 | |
Nitrogen | / | / | / | 0.7-0.8 | 1.1-1.3 | ||
30 | Air | / | / | / | 0.65 | 0.6-0.7 | |
Nitrogen | / | / | / | 0.25 | 0.33-0.35 | ||
35 | Nitrogen | / | / | / | / | / | |
40 | Nitrogen | / | / | / | 0.15 | 0.25 | |
50 | Nitrogen | / | / | / | 0.1 | 0.15 | |
60 | Nitrogen | / | / | / | / | 0.1 | |
70 | Nitrogen | / | / | / | / | 0.06 | |
80 | Nitrogen | / | / | / | / | / | |
90 | Nitrogen | / | / | / | / | / | |
100 | Nitrogen | / | / | / | / | / | |
Aluminum | Thickness(MM) | Gas | 1500W | 3000W | 6000W | 12000W | 15000W |
Speed (M/MIN) | Speed (M/MIN) | Speed (M/MIN) | Speed (M/MIN) | Speed (M/MIN) | |||
1 | Nitrogen/Air | 21-23 | 40-43 | 43-46 | / | / | |
2 | Nitrogen/Air | 5-7 | 16-18 | 26-28 | / | / | |
3 | Nitrogen/Air | 3.2-3.5 | 8-10 | 6-6.5 | 27-30 | 28-32 | |
4 | Nitrogen/Air | 1.5-1.7 | 5-6 | 4.5-5 | 19-21 | 20-22 | |
5 | Nitrogen/Air | 0.5-0.7 | / | 2.8-2.9 | 14-16 | 16-18 | |
6 | Nitrogen/Air | / | 1.5-2 | 1.7-1.8 | 10-12 | 12-14 | |
8 | Nitrogen/Air | / | 0.6-0.7 | 1.0-1.2 | 7-8 | 8-9 | |
10 | Nitrogen/Air | / | / | 0.7-0.9 | 4-5 | 5.5-6 | |
12 | Nitrogen/Air | / | / | 0.5-0.6 | 2.5-3 | 3.5-4 | |
14 | Nitrogen/Air | / | / | / | 2.3-2.5 | 2.5-3 | |
16 | Nitrogen/Air | / | / | / | 1.6-1.8 | 1.8-2 | |
18 | Nitrogen/Air | / | / | / | 1-1.2 | 1.4-1.6 | |
20 | Nitrogen/Air | / | / | / | 0.8 | 0.9-1.0 | |
22 | Nitrogen/Air | / | / | / | 0.5 | 0.8 | |
25 | Nitrogen/Air | / | / | / | / | 0.5 | |
30 | Nitrogen/Air | / | / | / | / | / | |
40 | Nitrogen/Air | / | / | / | / | / | |
50 | Nitrogen/Air | / | / | / | / | / | |
Brass | Thickness(MM) | Gas | 1500W | 3000W | 6000W | 12000W | 15000W |
Speed (M/MIN) | Speed (M/MIN) | Speed (M/MIN) | Speed (M/MIN) | Speed (M/MIN) | |||
1 | Nitrogen/Air | 18-20 | 37-40 | 41-43 | |||
2 | Nitrogen/Air | 4-5 | 14-16 | 24-26 | |||
3 | Nitrogen/Air | 2.3-2.5 | 7-9 | 13-14 | 25-28 | 25-29 | |
4 | Nitrogen/Air | 1.2-1.4 | 3-4 | 9-10 | 16-18 | 18-20 | |
5 | Nitrogen/Air | / | / | 5-6 | 12-14 | 13-16 | |
6 | Nitrogen/Air | / | 1.2-1.5 | 4-4.5 | 9-11 | 11-13 | |
8 | Nitrogen/Air | / | 0.5-0.6 | 2.3-2.5 | 6-7 | 7-8 | |
10 | Nitrogen/Air | / | / | 1.5-1.6 | 3.5-4.5 | 5-5.5 | |
12 | Nitrogen/Air | / | / | 1.0-1.2 | 2.2-2.8 | 3.2-3.5 | |
14 | Nitrogen/Air | / | / | 0.7-0.9 | 1.8-2 | 2.3-2.8 | |
16 | Nitrogen/Air | / | / | 0.5-0.6 | 1.4-1.6 | 1.5-1.8 | |
18 | Nitrogen/Air | / | / | / | 0.8-1.0 | 1.1-1.3 | |
20 | Nitrogen/Air | / | / | / | 0.7 | 0.7-0.9 | |
22 | Nitrogen/Air | / | / | / | 0.4 | 0.7 | |
25 | Nitrogen/Air | / | / | / | / | 0.4 | |
1. In the cutting data, the core diameter of the output fiber of the 1500W laser is 50 microns. | |||||||
2. This cutting data uses Jia qiang cutting head, and the optical ratio is 100/125(focallength of collimating focusing lens) . | |||||||
3. Cutting auxiiary gas:liquidoxygen(purity99.99%), liquid nitrogen(purity 99.999%) , air(oil, water and filtration) . | |||||||
4. The air pressure in this cutting data specifically refers to the monitored air pressure at the cutting head. | |||||||
5. Due to diference sin various equipment configurations and cutting processes(machine tools, water cooling, environment, cutting gas nozzles, gas pressure, etc.) used by different customers. | |||||||
6. All parameters are dynamic and for reference only. For more information, please contact customer service. |
The enclosed hydraulic exchange workbench ultra-high-power fiber laser cutting machine can be divided into the following systems:
The fully enclosed workbench system mainly provides a safe and enclosed working environment for operators. The design concept focuses on operator health and equipment maintenance. By fully enclosing the work area, it effectively prevents laser radiation and metal dust from escaping and protects the operator's health. At the same time, the fully enclosed design also helps to maintain a clean and tidy working environment, reducing maintenance costs.
The fully enclosed workbench system mainly consists of three parts: the fully enclosed workbench, the infeed port, and the outfeed port. The fully enclosed workbench is made of high-strength materials with features such as radiation protection, dust resistance, and ease of cleaning. The infeed port and outfeed port are designed on both sides of the workbench for convenient operator access and metal sheet placement.
During the operation process, operators place the metal sheets to be cut on the fully enclosed workbench surface and enter the work area through the infeed port. After the cutting is completed, the metal sheets are transported out of the work area through the outfeed port. In this process, the fully enclosed design ensures that laser radiation and metal dust do not escape and protects operator health.
Hydraulic automatic exchange workbench system, the core of which is a high-precision hydraulic system, is designed mainly to improve work efficiency and reduce manual intervention. In traditional working mode, operators need to manually replace the workbench, which not only reduces work efficiency but also easily leads to problems due to human errors. Therefore, the design purpose of this system is to achieve fast and accurate replacement of the workbench through automation, thereby improving work efficiency and reducing manual intervention.
The hydraulic automatic exchange workbench system is mainly composed of three parts: the hydraulic system, the exchange workbench, and the control system. The hydraulic system is the core of this system, which consists of a series of hydraulic cylinders, pipes, and controllers that are used to achieve automatic exchange of the workbench. The exchange workbench consists of multiple workbench surfaces, each of which can be used to place metal plate materials for cutting. The control system is used to control the operation of the hydraulic system to ensure that the replacement process of the workbench is accurate and error-free.
When the task on one workbench is completed, the control system will issue an instruction and start the hydraulic system. The hydraulic system will move the new workbench surface according to the instructions to the front of the equipment for operators to replace. This process is automatically completed without manual intervention. At the same time, the control system can also monitor in real time the operating status of the hydraulic system. If there is any abnormality, it will immediately issue an alarm and take corresponding protective measures.
The greatest advantage of the hydraulic automatic exchange workbench system is that it can greatly improve work efficiency. Through automation of workbench replacement, operators can continuously perform multiple tasks without frequent manual replacement of the workbench. At the same time, this system can also reduce manual intervention, reducing operator workload and improving work comfort.
The ultra-high-power fiber laser cutting system is the key component of the enclosed hydraulic exchange workbench ultra-high-power fiber laser cutting machine. It uses ultra-high-power fiber lasers to cut various metal plates with features such as high precision, high speed, and high efficiency, which can greatly improve the cutting quality and speed.
The ultra-high-power fiber laser is the core component of this system, and its types mainly include Yb-doped fiber lasers, Er-doped fiber lasers, etc. These lasers inject high-power lasers into the fiber to generate high-energy laser beams that achieve fast and accurate cutting of metal plates.
After processing by the cutting head and optical system, the high-energy laser beam generated by the ultra-high-power fiber laser forms a high-energy spot that acts on the surface of the metal plate. The metal plate within the spot range reaches the melting point instantly and forms a molten state. As the spot moves, the molten metal plate cools down quickly and forms a cut.
The ultra-high-power fiber laser cutting system has features such as high precision, high speed, and high efficiency. Firstly, due to the good beam quality of the fiber laser, the spot can be accurately applied to the surface of the metal plate, thereby forming a precise cut and edge. Secondly, the operating speed of the fiber laser is very fast, which enables high-speed cutting and improves production efficiency. Additionally, the energy conversion efficiency of the fiber laser is high, which can reduce energy consumption.
To protect the fiber laser and cutting system, a series of protective measures are usually taken. For example, during the cutting process, cooling methods such as water cooling or air cooling can be used to cool the fiber laser to avoid overheating and damage. In addition, protective functions such as automatic power off and automatic shutdown can be added to the cutting system to protect its safety and stable operation.
The control system is responsible for coordinating and monitoring the entire cutting process. Its main function is to automatically adjust the laser power, speed, and cutting head position according to the parameters input by the operator, to ensure that the cutting accuracy and effect meet the requirements. At the same time, the control system can also monitor the operational status of the equipment in real time, and if there is any abnormality, it will immediately issue an alarm and take corresponding protective measures.
The control system is mainly composed of a computer, data acquisition card, sensors, actuators, and alarm devices. The computer acts as the core of the control system, responsible for data processing, logical operations, and parameter adjustments. The data acquisition card is used to collect status data from the laser, speed controller, and cutting head equipment. Sensors are used to monitor the operational status of the equipment and transmit monitoring data to the computer. Actuators are used to control the actions of the laser, speed controller, and cutting head. Alarm devices issue alarms when equipment abnormalities occur.
During the operation process, operators input information such as the size, thickness, and material of the metal plate to be cut through the control system interface. The control system automatically adjusts the laser power, speed, and cutting head position based on this information to ensure cutting accuracy and effectiveness. At the same time, the control system monitors the operational status of the equipment in real time through sensors, such as laser current and speed controller speed. When abnormal data is monitored, the control system will immediately issue an alarm and take corresponding protective measures such as automatically shutting off the laser and stopping movement.
The advantage of the control system lies in its ability to automatically adjust the laser power, speed, and cutting head position according to operator-input parameters, which improves cutting accuracy and effectiveness. At the same time, its ability to monitor equipment operation status in real time can timely detect abnormal situations and take protective measures to avoid equipment damage and production accidents.
Share with
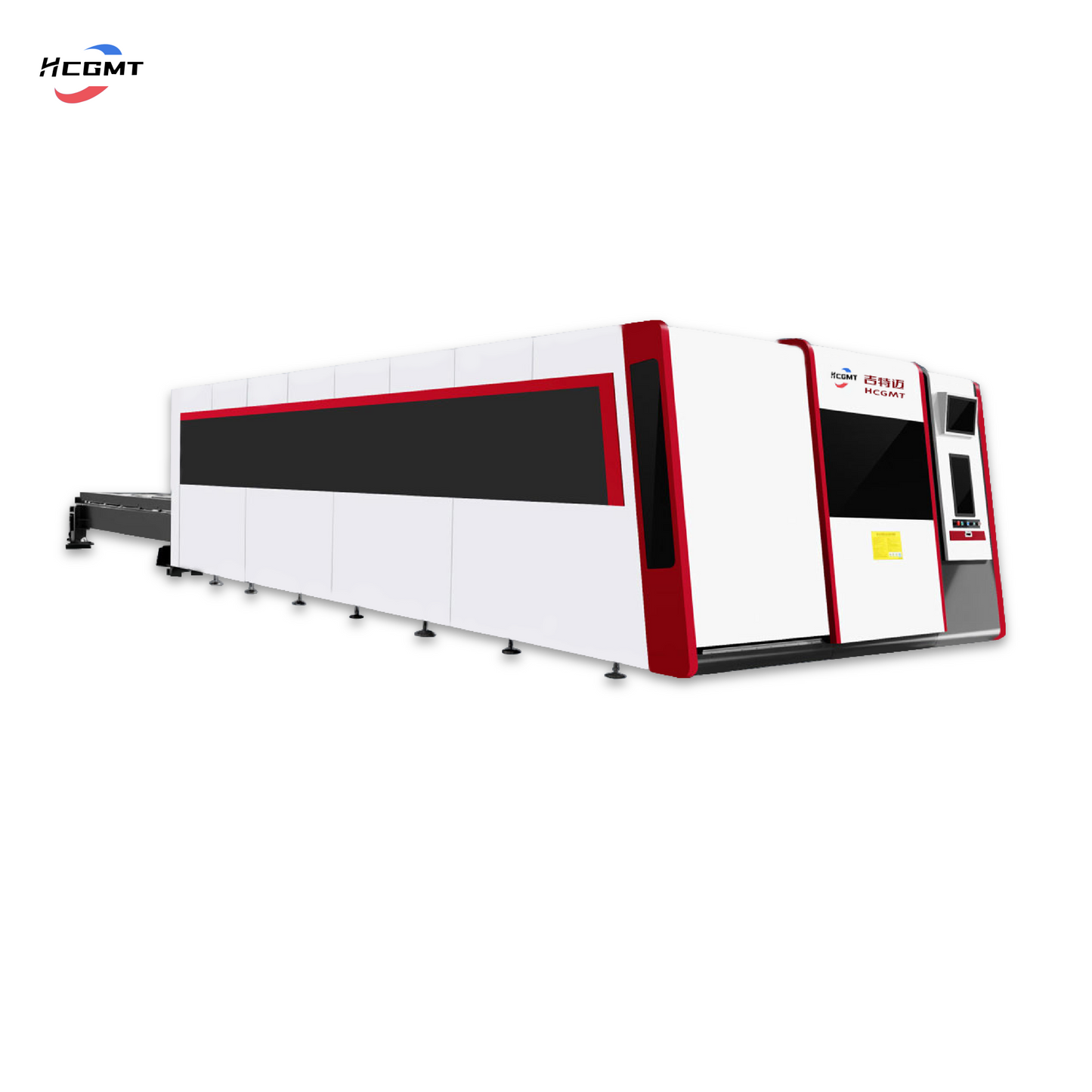
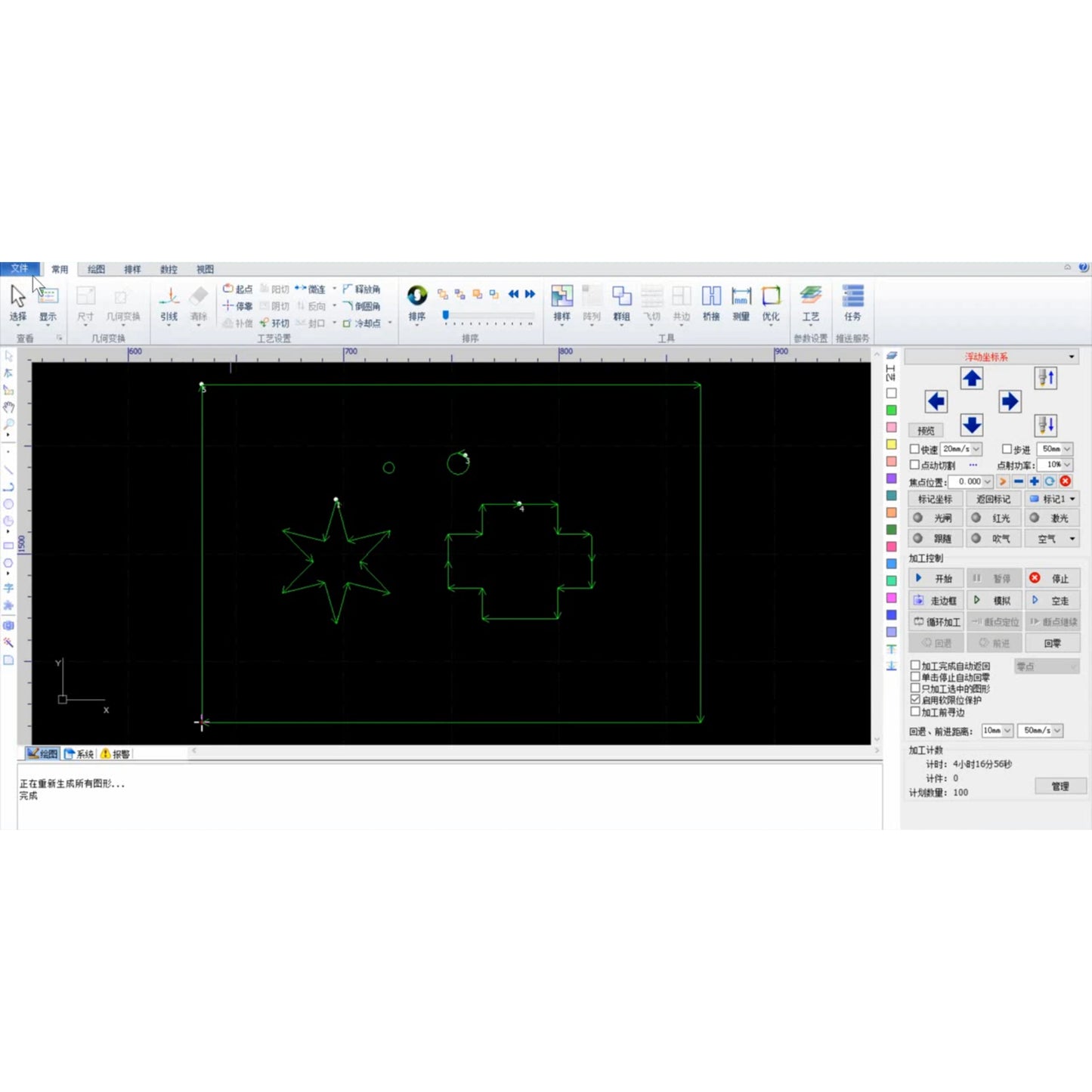
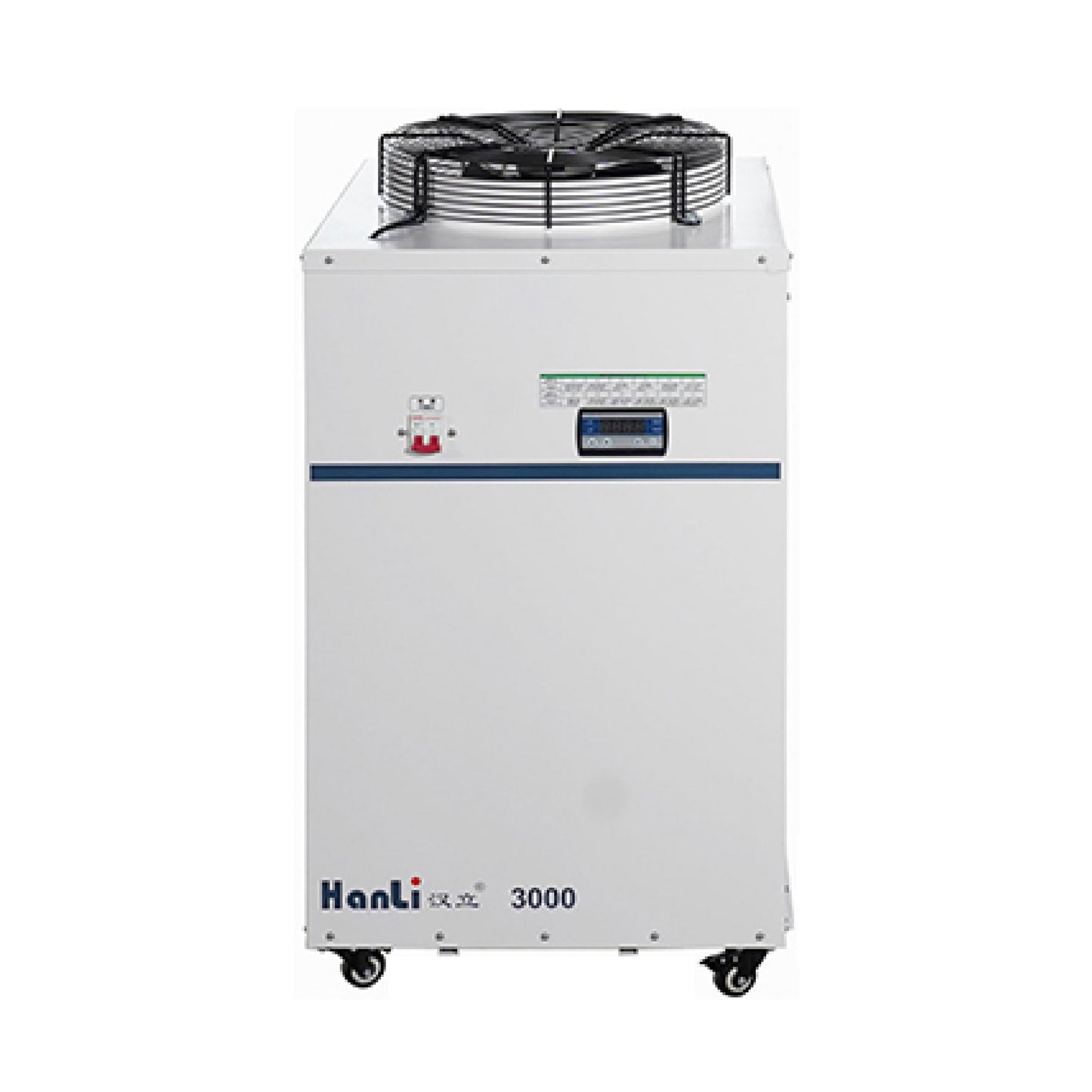
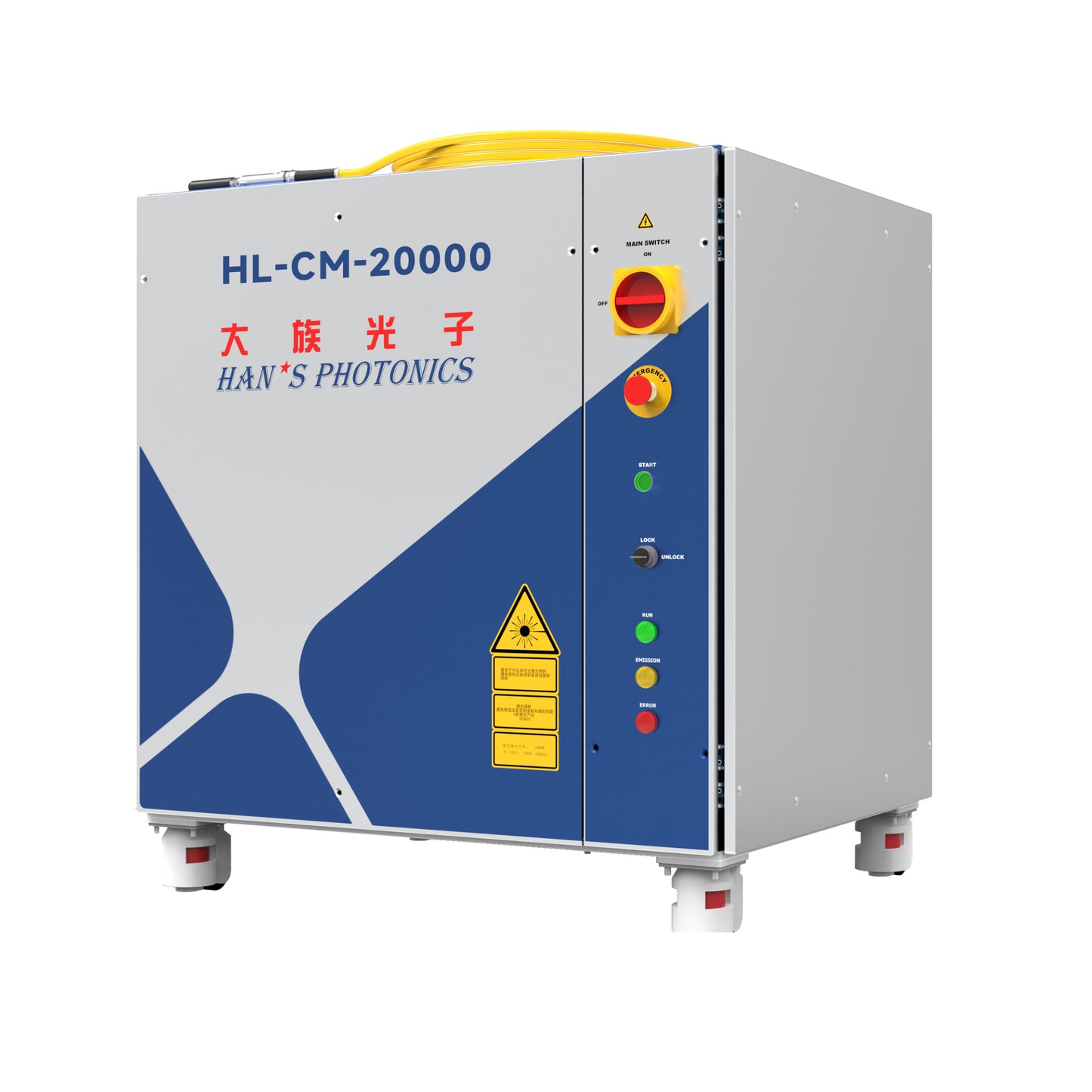
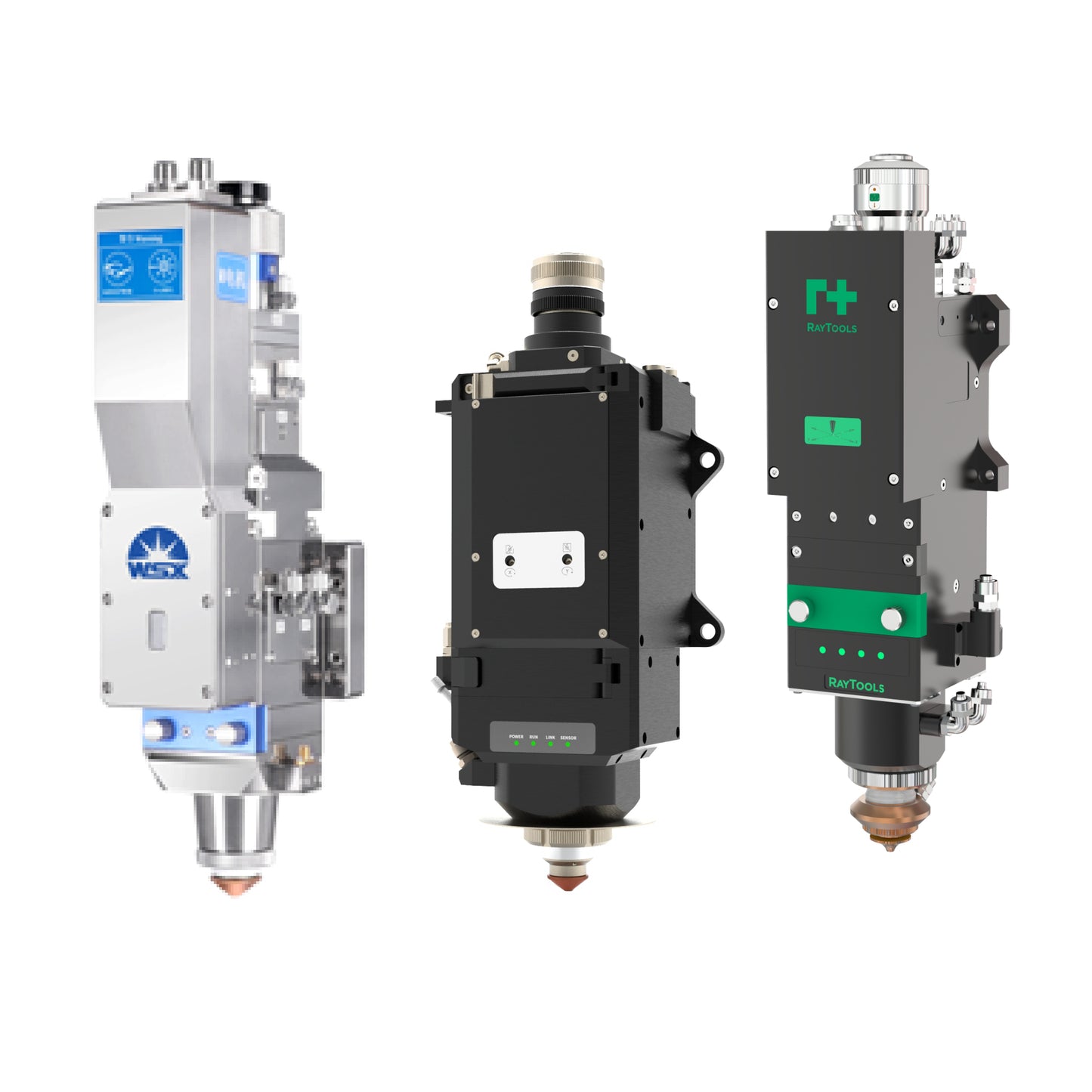
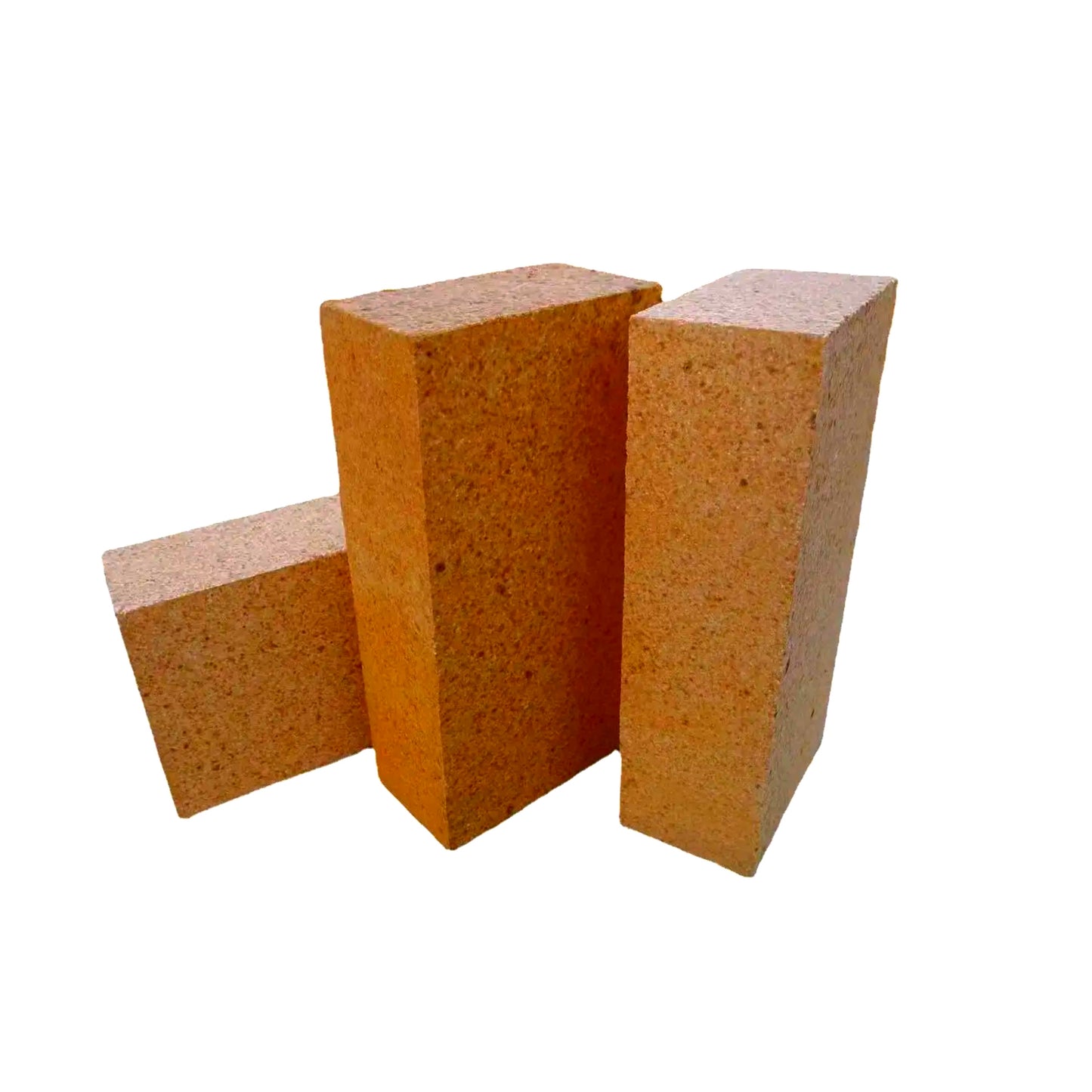