Компания JTM Intelligent Equipment Co., Ltd.
Гидравлический токарный станок для лазерной резки с двойным верстаком
Гидравлический токарный станок для лазерной резки с двойным верстаком
Технические параметры станка для лазерной резки высокой мощности с двойным рабочим столом JTM с гидравлическим переключением |
|
Мощность лазера | 15000Вт/20000Вт/30000Вт |
Максимальный диапазон резки | 6*2,5 м/8*2,5 м/12*2,5 м |
Максимальная скорость движения | 150М/МИН |
Максимальное ускорение | 1,5G |
Точность позиционирования | ±0,05 мм |
Точность изменения положения | ±0,02 мм |
Рабочее напряжение | 380 В/50 Гц |
Тип охлаждения | Водяное охлаждение |
Примечание. Все параметры являются динамическими и предназначены только для справки. Для получения дополнительной информации, пожалуйста, свяжитесь со службой поддержки клиентов. |
Толщина резки и параметры скорости | |||||||
Материал | Толщина (ММ) | Газ | 1500 Вт | 3000 Вт | 6000 Вт | 12000 Вт | 15000 Вт |
Углеродистая сталь (Q235B) | Скорость (М/МИН) | Скорость (М/МИН) | Скорость (М/МИН) | Скорость (М/МИН) | Скорость (М/МИН) | ||
1 | Азот/Кислород | 26-29 | 47-50 | 58-62 | |||
2 | Азот/Кислород | 7-8 | 21-23 | 31-36 | |||
3 | Азот/Кислород | / | 6-12 | 18-22 | 32-38 | 34-39 | |
Кислород | 2,9-3,2 | 3,9-4,1 | / | / | / | ||
4 | Азот/Кислород | / | / | 11-13 | 22-26 | 25-29 | |
Кислород | 2,4-2,6 | 3,4-3,6 | 3.7-4 | / | / | ||
5 | Азот/Кислород | / | / | 8-10 | 17-20 | 18-22 | |
Кислород | 1,8-2,0 | / | 3,2-3,3 | / | / | ||
6 | Воздух | / | / | 5,5-6,5 | 12-14 | 16-18 | |
Азот | / | / | 5,5-6,5 | 11-13 | 15-17 | ||
Кислород | 1,6-1,8 | 2,7-2,8 | 2,6-2,8 | 2,6-2,8 | 2,6-2,8 | ||
8 | Воздух | / | / | / | 8-10 | 10-11 | |
Азот | / | / | / | 7-9 | 9-10 | ||
Кислород | 1,1-1,3 | 2,1-2,3 | 2,5-2,6 | 2,5-2,6 | 2,5-2,6 | ||
10 | Воздух | / | / | / | 5-6 | 7-8 | |
Азот | / | / | / | 4,5-5,5 | 6,5-7 | ||
Кислород | 0,9-1,0 | 1,4-1,6 | 2,2-2,3 | 2,2-2,3 | 2,2-2,3 | ||
12 | Воздух | / | / | / | 4.2-5 | 5,5-6,5 | |
Азот | / | / | / | 4-4,8 | 5-6 | ||
Кислород | 0,8-0,9 | 1-1,1 | 1,8-2,0 | 1,9-2 | 1,9-2 | ||
14 | Воздух | / | / | / | 3,5-4,2 | 5-5,55 | |
Азот | / | / | / | 3,2-3,5 | 4,8~5 | ||
Кислород | 0,6-0,7 | 0,9-0,95 | 1,4-1,7 | 1,5-1,6 | 1,5-1,6 | ||
16 | Воздух | / | / | / | / | / | |
Кислород | 0,5-0,6 | 0,8-0,95 | 1,2-1,3 | 1,4-1,6 | 1,4-1,6 | ||
18 | Воздух | / | / | / | / | / | |
Кислород | / | 0,7-0,72 | 0,7-0,8 | 1,4-1,5 | 1,4-1,5 | ||
20 | Воздух | / | / | / | / | / | |
Кислород | / | 0,6-0,65 | 0,6-0,65 | 1,4-1,5 | 1,4-1,5 | ||
22 | Кислород | / | 0,55 | 0,55-0,6 | 1.2 | 1,2-1,3 | |
25 | Кислород | / | 0,5 | 0,5-0,55 | 1 | 1,2-1,3 | |
30 | Кислород | / | / | / | 0,4 | 0,8~0,9 | |
35 | Кислород | / | / | / | 0,35 | 0,4 | |
40 | Кислород | / | / | / | 0,3 | 0,35 | |
45 | Кислород | / | / | / | 0,2 | 0,25 | |
50 | Кислород | / | / | / | / | 0,2 | |
60 | Кислород | / | / | / | / | / | |
70 | Кислород | / | / | / | / | / | |
80 | Кислород | / | / | / | / | / | |
Нержавеющая сталь (SUS 304) | Толщина (ММ) | Газ | 1500 Вт | 3000 Вт | 6000 Вт | 12000 Вт | 15000 Вт |
Скорость (М/МИН) | Скорость (М/МИН) | Скорость (М/МИН) | Скорость (М/МИН) | Скорость (М/МИН) | |||
1 | Азот/Кислород | 27-30 | 50-53 | 59-65 | / | / | |
2 | Азот/Кислород | 8-9 | 23-25 | 32-38 | / | / | |
3 | Азот/Кислород | 4,2-4,5 | 10-12 | 20-24 | 32-38 | 34-39 | |
4 | Азот/Кислород | 2,0-2,2 | 6-8 | 12-15 | 22-26 | 25-29 | |
5 | Азот/Кислород | 1,5-1,7 | / | 9-11 | 17-20 | 18-22 | |
6 | Воздух | 1,0-1,2 | 2,9-3,1 | 6-7,5 | 14-16 | 17-20 | |
Азот | 1,0-1,2 | 2,9-3,1 | 6-7,5 | 13-15 | 16-19 | ||
8 | Воздух | 0,5-0,6 | 1,2-1,3 | 4-4,5 | 10-12 | 12-14 | |
Азот | 0,5-0,6 | 1,2-1,3 | 4-4,5 | 9-11 | 11-13 | ||
10 | Воздух | / | 0,75-0,8 | 2,2-2,4 | 8-9 | 8-10 | |
Азот | / | 0,75-0,8 | 2,2-2,4 | 7,5-8 | 7-9 | ||
12 | Воздух | / | 0,5 | 1,3-1,5 | 6,0-6,5 | 7,0-7,5 | |
Азот | / | 0,5 | 1,3-1,5 | 5,2-6,0 | 6,0-6,5 | ||
14 | Воздух | / | / | 0,9-1,0 | 3,7-4,0 | 4,8-5,0 | |
Азот | / | / | 0,9-1,0 | 3,2-3,5 | 4,3-4,5 | ||
16 | Воздух | / | / | 0,8-0,85 | 2,7-3,0 | 3,4-3,8 | |
Азот | / | / | 0,8-0,85 | 2,3-2,5 | 3,0-3,5 | ||
18 | Воздух | / | / | / | 2,2-2,5 | 3,0-3,3 | |
Азот | / | / | / | 1,8-2,0 | 2,6-2,8 | ||
20 | Воздух | / | / | 0,5-0,6 | 1,6-1,8 | 2,0-2,2 | |
Азот | / | / | 0,5-0,6 | 1,3-1,5 | 1,6-1,8 | ||
25 | Воздух | / | / | / | 0,8-1,0 | 1,2-1,5 | |
Азот | / | / | / | 0,7-0,8 | 1,1-1,3 | ||
30 | Воздух | / | / | / | 0,65 | 0,6-0,7 | |
Азот | / | / | / | 0,25 | 0,33-0,35 | ||
35 | Азот | / | / | / | / | / | |
40 | Азот | / | / | / | 0,15 | 0,25 | |
50 | Азот | / | / | / | 0,1 | 0,15 | |
60 | Азот | / | / | / | / | 0,1 | |
70 | Азот | / | / | / | / | 0,06 | |
80 | Азот | / | / | / | / | / | |
90 | Азот | / | / | / | / | / | |
100 | Азот | / | / | / | / | / | |
Алюминий | Толщина (ММ) | Газ | 1500 Вт | 3000 Вт | 6000 Вт | 12000 Вт | 15000 Вт |
Скорость (М/МИН) | Скорость (М/МИН) | Скорость (М/МИН) | Скорость (М/МИН) | Скорость (М/МИН) | |||
1 | Азот/Воздух | 21-23 | 40-43 | 43-46 | / | / | |
2 | Азот/Воздух | 5-7 | 16-18 | 26-28 | / | / | |
3 | Азот/Воздух | 3,2-3,5 | 8-10 | 6-6,5 | 27-30 | 28-32 | |
4 | Азот/Воздух | 1,5-1,7 | 5-6 | 4,5-5 | 19-21 | 20-22 | |
5 | Азот/Воздух | 0,5-0,7 | / | 2,8-2,9 | 14-16 | 16-18 | |
6 | Азот/Воздух | / | 1,5-2 | 1,7-1,8 | 10-12 | 12-14 | |
8 | Азот/Воздух | / | 0,6-0,7 | 1,0-1,2 | 7-8 | 8-9 | |
10 | Азот/Воздух | / | / | 0,7-0,9 | 4-5 | 5,5-6 | |
12 | Азот/Воздух | / | / | 0,5-0,6 | 2,5-3 | 3,5-4 | |
14 | Азот/Воздух | / | / | / | 2,3-2,5 | 2,5-3 | |
16 | Азот/Воздух | / | / | / | 1,6-1,8 | 1,8-2 | |
18 | Азот/Воздух | / | / | / | 1-1,2 | 1,4-1,6 | |
20 | Азот/Воздух | / | / | / | 0,8 | 0,9-1,0 | |
22 | Азот/Воздух | / | / | / | 0,5 | 0,8 | |
25 | Азот/Воздух | / | / | / | / | 0,5 | |
30 | Азот/Воздух | / | / | / | / | / | |
40 | Азот/Воздух | / | / | / | / | / | |
50 | Азот/Воздух | / | / | / | / | / | |
Латунь | Толщина (ММ) | Газ | 1500 Вт | 3000 Вт | 6000 Вт | 12000 Вт | 15000 Вт |
Скорость (М/МИН) | Скорость (М/МИН) | Скорость (М/МИН) | Скорость (М/МИН) | Скорость (М/МИН) | |||
1 | Азот/Воздух | 18-20 | 37-40 | 41-43 | |||
2 | Азот/Воздух | 4-5 | 14-16 | 24-26 | |||
3 | Азот/Воздух | 2,3-2,5 | 7-9 | 13-14 | 25-28 | 25-29 | |
4 | Азот/Воздух | 1,2-1,4 | 3-4 | 9-10 | 16-18 | 18-20 | |
5 | Азот/Воздух | / | / | 5-6 | 12-14 | 13-16 | |
6 | Азот/Воздух | / | 1,2-1,5 | 4-4,5 | 9-11 | 11-13 | |
8 | Азот/Воздух | / | 0,5-0,6 | 2,3-2,5 | 6-7 | 7-8 | |
10 | Азот/Воздух | / | / | 1,5-1,6 | 3,5-4,5 | 5-5,5 | |
12 | Азот/Воздух | / | / | 1,0-1,2 | 2,2-2,8 | 3,2-3,5 | |
14 | Азот/Воздух | / | / | 0,7-0,9 | 1,8-2 | 2,3-2,8 | |
16 | Азот/Воздух | / | / | 0,5-0,6 | 1,4-1,6 | 1,5-1,8 | |
18 | Азот/Воздух | / | / | / | 0,8-1,0 | 1,1-1,3 | |
20 | Азот/Воздух | / | / | / | 0,7 | 0,7-0,9 | |
22 | Азот/Воздух | / | / | / | 0,4 | 0,7 | |
25 | Азот/Воздух | / | / | / | / | 0,4 | |
1. В данных резки диаметр сердцевины выходного волокна лазера мощностью 1500 Вт составляет 50 микрон. | |||||||
2. В данных режимах резки используется режущая головка Jia qiang, а оптическое соотношение составляет 100/125 (фокусное расстояние коллимирующей фокусирующей линзы). | |||||||
3. Режущий вспомогательный газ: жидкий кислород (чистота 99,99%), жидкий азот (чистота 99,999%), воздух (масло, вода и фильтрация). | |||||||
4. Давление воздуха в этих данных резки относится конкретно к контролируемому давлению воздуха на режущей головке. | |||||||
5. Из-за различий в конфигурациях оборудования и процессах резки (станки, водяное охлаждение, окружающая среда, сопла режущего газа, давление газа и т. д.), используемые разными клиентами. | |||||||
6. Все параметры являются динамическими и предназначены только для справки. Для получения дополнительной информации, пожалуйста, свяжитесь со службой поддержки клиентов. |
Закрытый гидравлический сменный станок сверхмощной волоконной лазерной резки можно разделить на следующие системы:
Полностью закрытая система рабочего места в основном обеспечивает безопасную и закрытую рабочую среду для операторов. Концепция дизайна ориентирована на здоровье операторов и техническое обслуживание оборудования. Полностью закрывая рабочую зону, он эффективно предотвращает выход лазерного излучения и металлической пыли и защищает здоровье оператора. В то же время полностью закрытая конструкция помогает поддерживать чистоту и порядок на рабочем месте, сокращая затраты на техническое обслуживание.
Полностью закрытый верстак в основном состоит из трех частей: полностью закрытый верстак, входной порт и выходной порт. Полностью закрытый верстак изготовлен из высокопрочных материалов и обладает такими характеристиками, как радиационная защита, пыленепроницаемость и простота очистки. Входной и выходной порты расположены с обеих сторон рабочего места для удобного доступа оператора и размещения листового металла.
Во время рабочего процесса операторы кладут металлические листы, подлежащие резке, на полностью закрытую поверхность верстака и входят в рабочую зону через подающее отверстие. После завершения резки металлические листы вывозятся из рабочей зоны через разгрузочное отверстие. При этом полностью закрытая конструкция предотвращает утечку лазерного излучения и металлической пыли и защищает здоровье оператора.
Гидравлическая система автоматического обмена станков, ядром которой является высокоточная гидравлическая система, предназначена главным образом для повышения эффективности работы и уменьшения ручного вмешательства. В традиционном режиме работы операторам приходится вручную заменять верстак, что не только снижает эффективность работы, но и легко приводит к проблемам из-за человеческих ошибок. Таким образом, цель разработки этой системы — добиться быстрой и точной замены рабочего места за счет автоматизации, тем самым повышая эффективность работы и сокращая ручное вмешательство.
Гидравлическая система автоматического сменного рабочего места в основном состоит из трех частей: гидравлической системы, сменного рабочего места и системы управления. Гидравлическая система является ядром этой системы, которая состоит из ряда гидравлических цилиндров, труб и контроллеров, которые используются для автоматической замены рабочего места. Сменный верстак состоит из нескольких поверхностей, на каждой из которых можно размещать металлические пластины для резки. Система управления используется для контроля работы гидравлической системы, чтобы обеспечить точность и безошибочность процесса замены верстака.
Когда задача на одном верстаке будет выполнена, система управления выдаст команду и запустит гидросистему. Гидравлическая система переместит новую поверхность рабочего места в соответствии с инструкциями к передней части оборудования, чтобы операторы могли его заменить. Этот процесс выполняется автоматически без ручного вмешательства. В то же время система управления также может отслеживать в режиме реального времени рабочее состояние гидравлической системы. В случае возникновения каких-либо отклонений он немедленно подаст сигнал тревоги и примет соответствующие защитные меры.
Самым большим преимуществом гидравлической автоматической сменной системы рабочего места является то, что она может значительно повысить эффективность работы. Благодаря автоматизации замены верстака операторы могут непрерывно выполнять несколько задач без частой замены верстака вручную. В то же время эта система также может сократить ручное вмешательство, снижая нагрузку на оператора и повышая комфорт работы.
Система сверхмощной волоконной лазерной резки является ключевым компонентом закрытого гидравлического сменного станка сверхмощной волоконной лазерной резки. Он использует сверхмощные волоконные лазеры для резки различных металлических пластин с такими характеристиками, как высокая точность, высокая скорость и высокая эффективность, что может значительно улучшить качество и скорость резки.
Сверхмощный волоконный лазер является основным компонентом этой системы, и его типы в основном включают волоконные лазеры с легированием Yb, волоконные лазеры с легированием Er и т. д. Эти лазеры вводят мощные лазеры в волокно для генерации высокоэнергетических лазеров. лазерные лучи, позволяющие быстро и точно резать металлические пластины.
После обработки режущей головкой и оптической системой высокоэнергетический лазерный луч, генерируемый сверхмощным волоконным лазером, образует высокоэнергетическое пятно, которое воздействует на поверхность металлической пластины. Металлическая пластина в пределах пятна мгновенно достигает точки плавления и переходит в расплавленное состояние. По мере движения пятна расплавленная металлическая пластина быстро остывает и образует разрез.
Система сверхмощной волоконной лазерной резки обладает такими характеристиками, как высокая точность, высокая скорость и высокая эффективность. Во-первых, благодаря хорошему качеству луча волоконного лазера пятно можно точно нанести на поверхность металлической пластины, тем самым формируя точный разрез и кромку. Во-вторых, скорость работы волоконного лазера очень высока, что обеспечивает высокоскоростную резку и повышает эффективность производства. Кроме того, эффективность преобразования энергии волоконного лазера высока, что позволяет снизить энергопотребление.
Для защиты волоконного лазера и системы резки обычно принимается ряд защитных мер. Например, в процессе резки для охлаждения волоконного лазера можно использовать такие методы охлаждения, как водяное или воздушное охлаждение, чтобы избежать перегрева и повреждения. Кроме того, в систему резки можно добавить защитные функции, такие как автоматическое отключение питания и автоматическое отключение, чтобы обеспечить ее безопасность и стабильную работу.
Система управления отвечает за координацию и контроль всего процесса резки. Его основная функция — автоматическая регулировка мощности, скорости и положения режущей головки лазера в соответствии с параметрами, введенными оператором, чтобы гарантировать, что точность и эффект резки соответствуют требованиям. При этом система управления также может отслеживать рабочее состояние оборудования в режиме реального времени и в случае возникновения каких-либо отклонений немедленно подаст сигнал тревоги и примет соответствующие защитные меры.
Система управления в основном состоит из компьютера, карты сбора данных, датчиков, исполнительных механизмов и устройств сигнализации. Компьютер выступает в роли ядра системы управления, отвечая за обработку данных, логические операции и настройку параметров. Карта сбора данных используется для сбора данных о состоянии лазера, регулятора скорости и оборудования режущей головки. Датчики используются для контроля рабочего состояния оборудования и передачи данных мониторинга на компьютер. Исполнительные механизмы используются для управления действиями лазера, регулятора скорости и режущей головки. Устройства сигнализации выдают сигналы тревоги при возникновении сбоев в работе оборудования.
В процессе работы операторы вводят такую информацию, как размер, толщина и материал металлической пластины, которую нужно разрезать, через интерфейс системы управления. Система управления автоматически регулирует мощность лазера, скорость и положение режущей головки на основе этой информации, чтобы обеспечить точность и эффективность резки. При этом система управления контролирует рабочее состояние оборудования в режиме реального времени с помощью датчиков, таких как ток лазера и регулятор скорости. При обнаружении аномальных данных система управления немедленно подает сигнал тревоги и принимает соответствующие защитные меры, такие как автоматическое отключение лазера и остановка движения.
Преимущество системы управления заключается в ее способности автоматически регулировать мощность лазера, скорость и положение режущей головки в соответствии с введенными оператором параметрами, что повышает точность и эффективность резки. В то же время его способность отслеживать состояние работы оборудования в режиме реального времени позволяет своевременно обнаруживать нештатные ситуации и принимать защитные меры во избежание повреждения оборудования и аварий на производстве.
Поделиться с
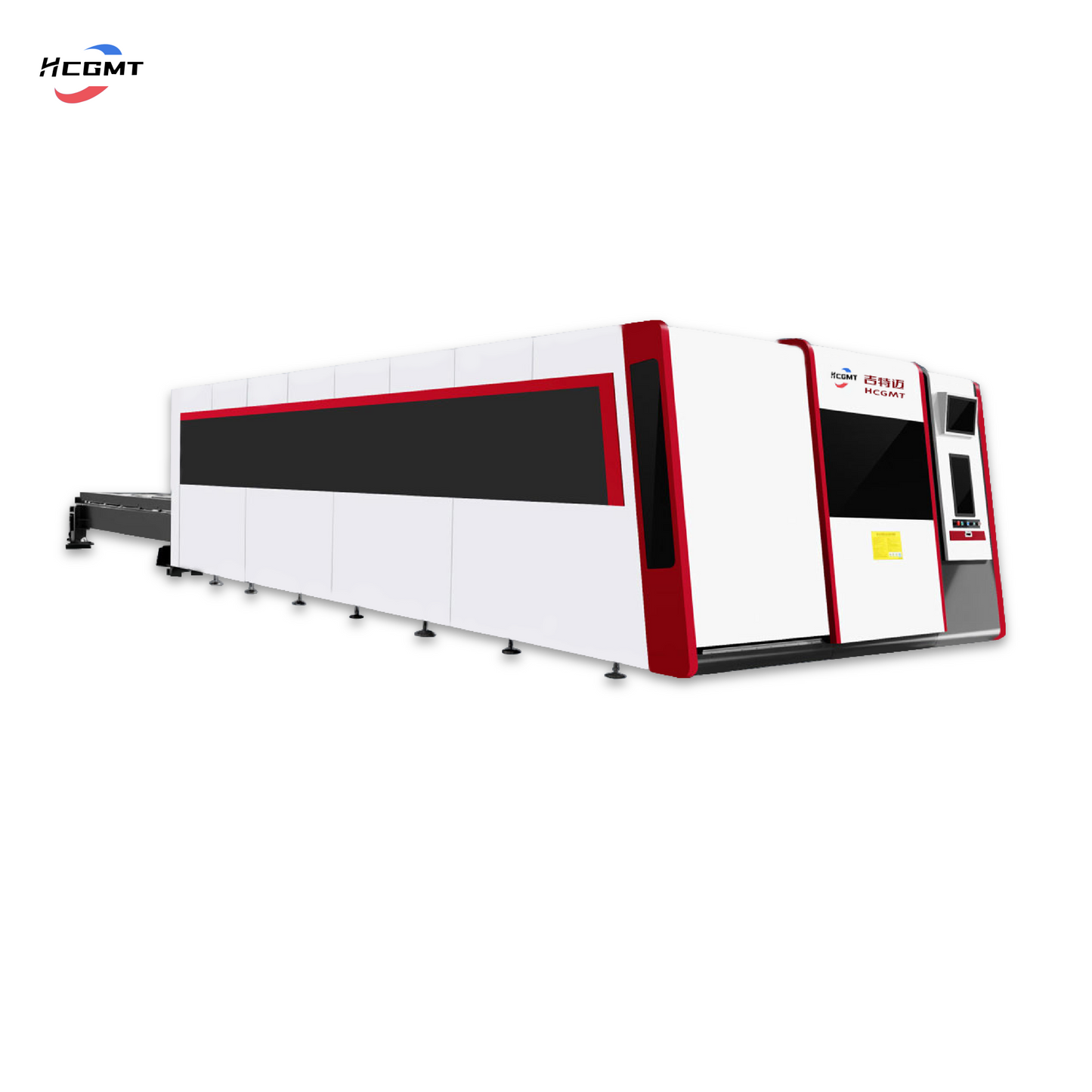
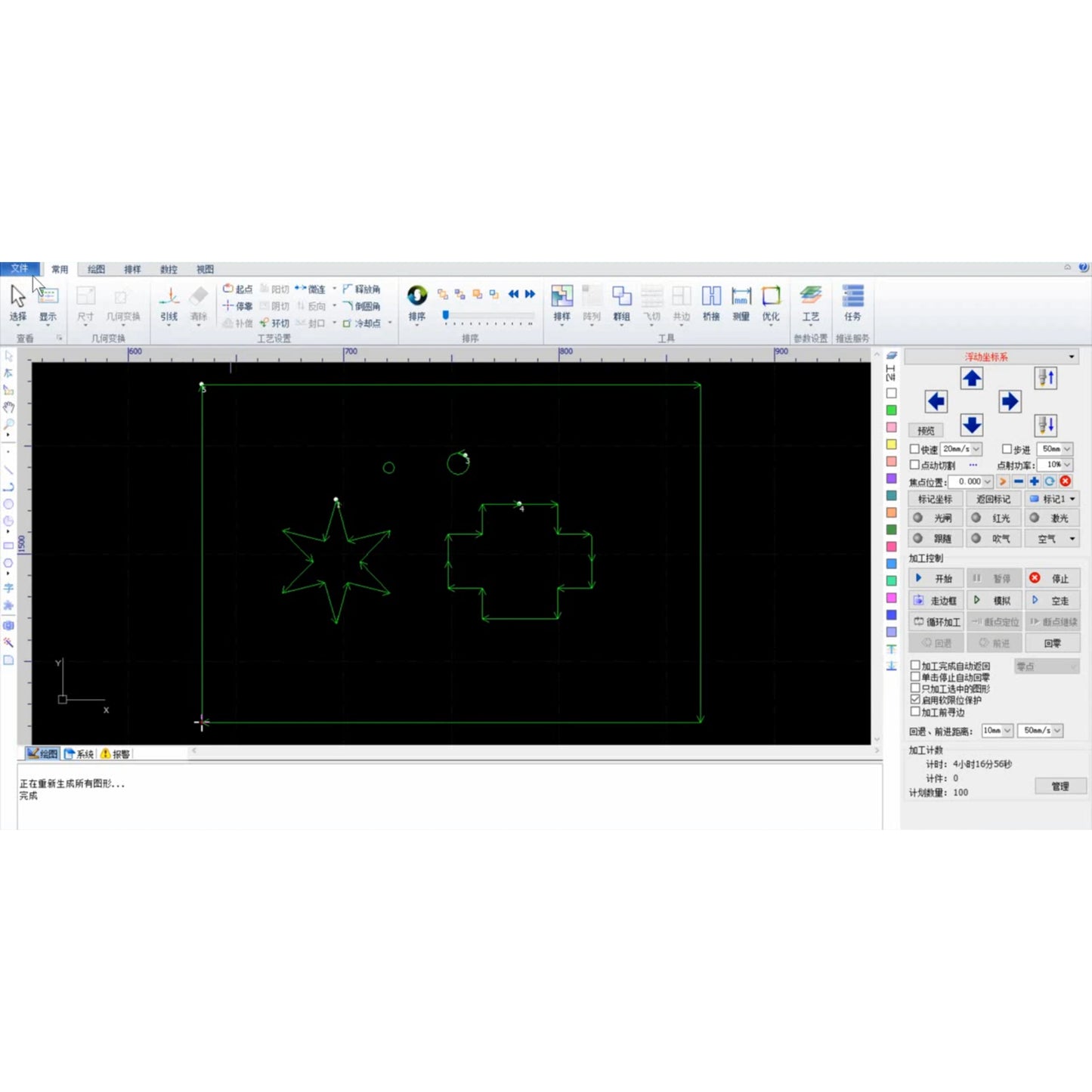
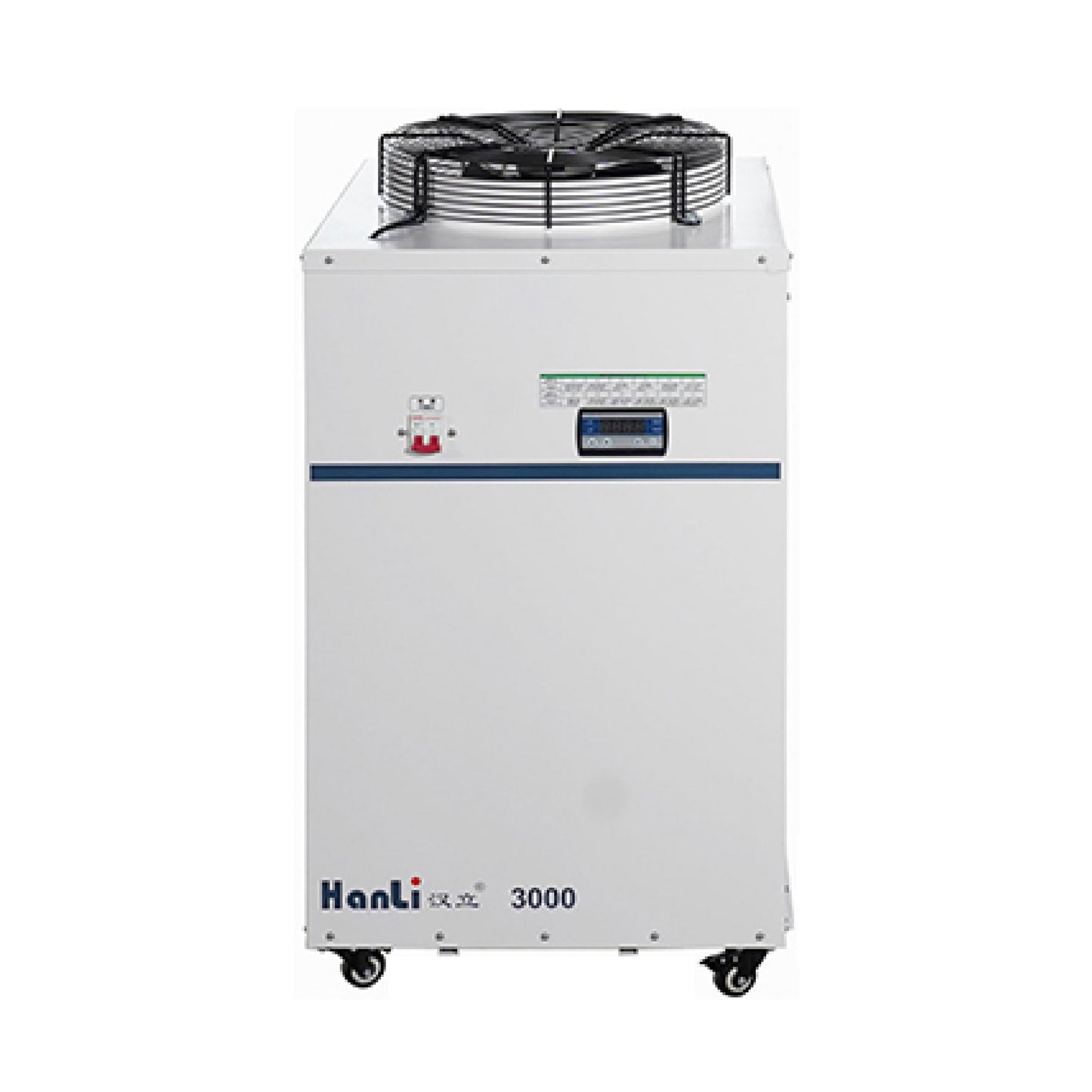
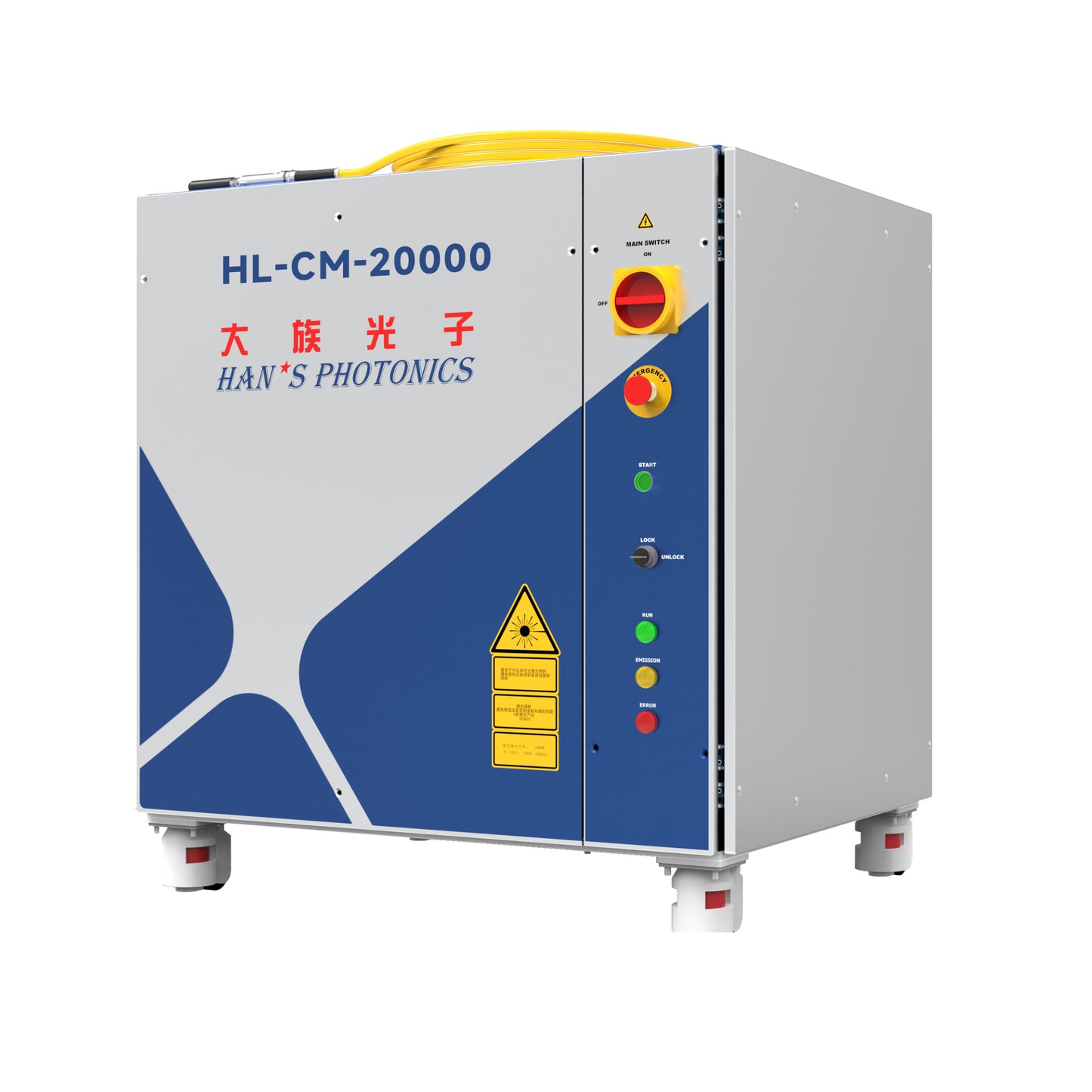
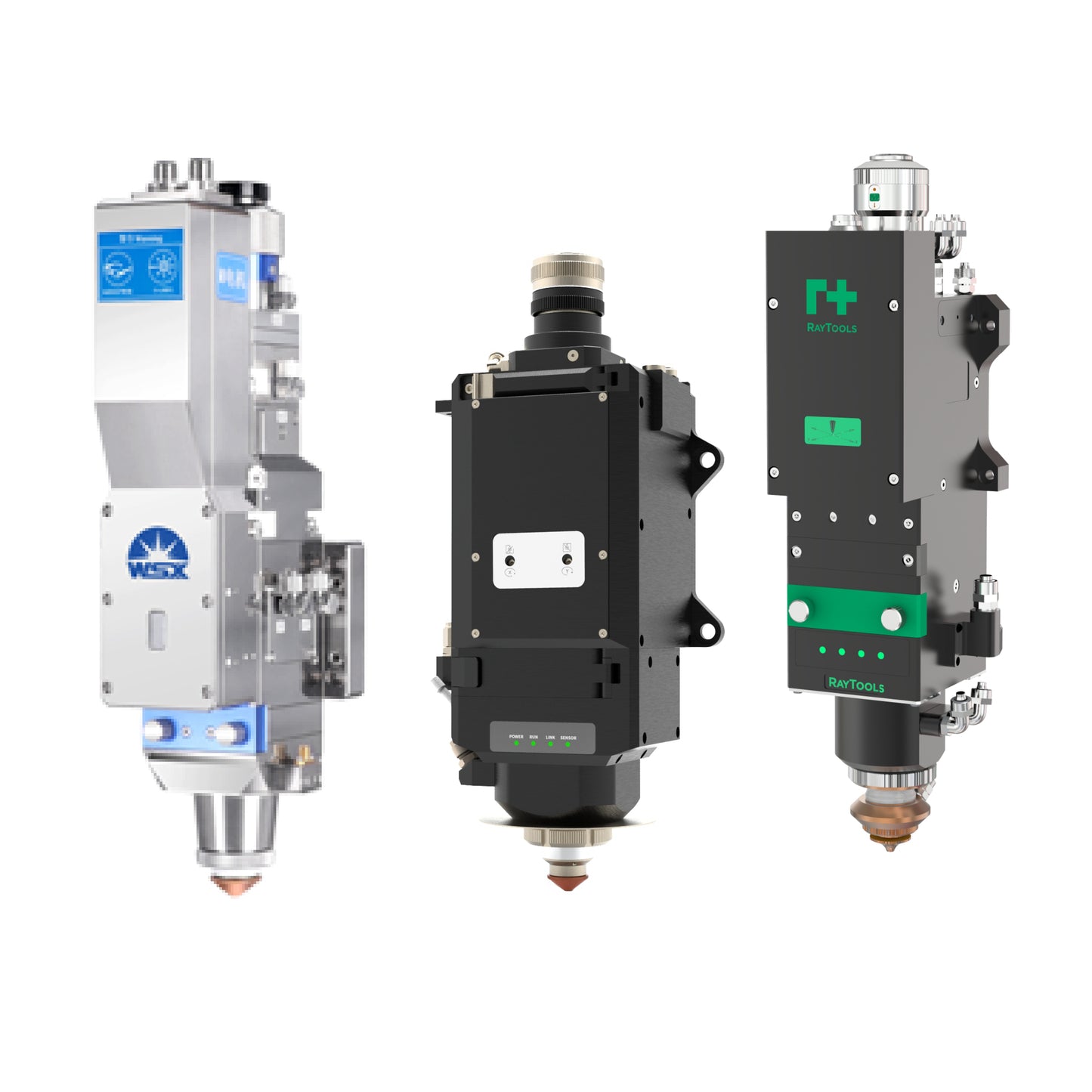
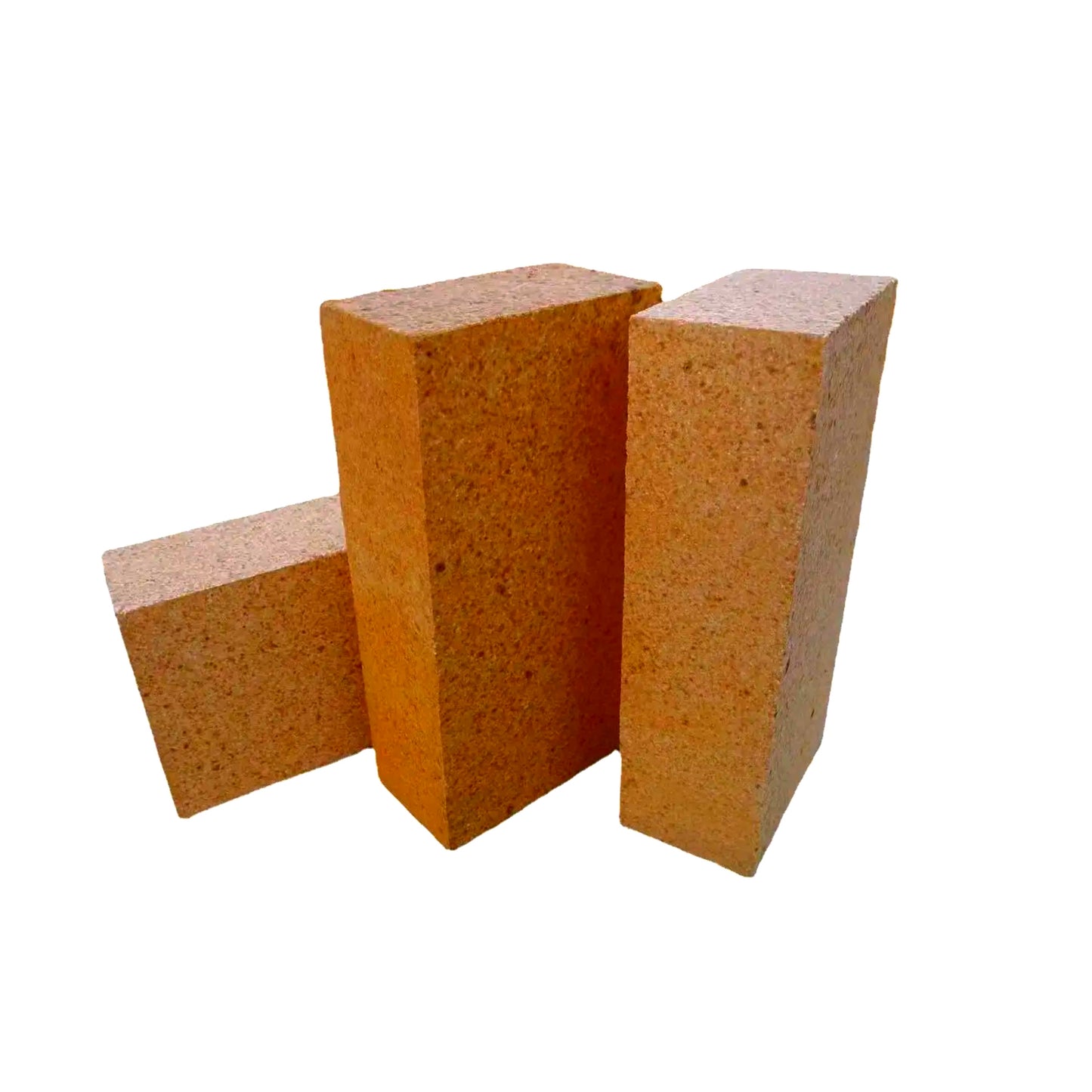